From BCN3D, Lithography 3D Printing With No Vat Brings Bigger Scale Plus Viscous Materials
Parts take shape in the open air. Viscous resin is rapidly carried on a laminate to build each layer. LCD screen size, not vat size, is the limit on productivity.
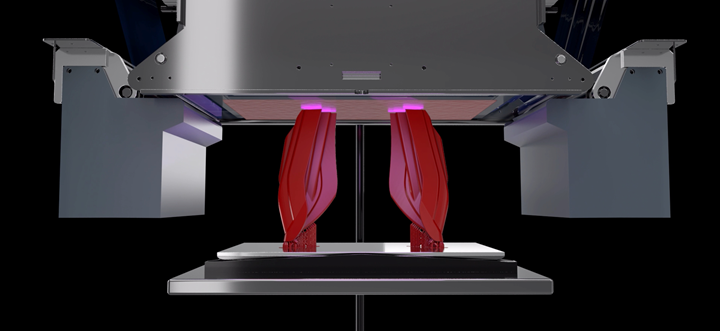
In the VLM process, material carried by a laminate fuses to the part to form the next layer. The part takes shape in the open air, unlike other lithography processes. Image courtesy of BCN3D.
3D printing technology provider BCN3D announced a new polymer additive manufacturing process it is calling Viscous Lithography Manufacturing (VLM). The process is similar to digital light processing in that it uses light to solidify a layer of material all at once, with the major difference that part formation does not take place within a resin vat. Material is carried to the part on a moving laminate instead. Two important consequences are: (1) much more viscous resins can now be used in a lithography process (because recirculation of resin within the vat is no longer a concern) and (2) build volume is now scalable without any consideration of vat size limitations. Build volume is instead determined by the size of the LCD screen solidifying each layer.
As a result, greater material freedom meets greater productivity. BCN3D CEO Xavier Faneca expressed what he sees as the import of this advance: “If 3D printing is to be the future of manufacturing, and what leads us towards local production, customization, control of supply chains and sustainability, all the players in the industry should be pushing in this direction.” VLM is his company’s move toward this goal, he says. “We want to show 3D printing in a new light so that it becomes the pivotal point of manufacturing.”
BCN3D is a 3D printer maker based in Spain currently providing fused filament fabrication (FFF) systems. In a recent press conference, Faneca and company CTO Eric Pallarés announced the new VLM technology, which they say is the result of three years of R&D.
Benefits of VLM
Instead of holding resin in a vat, the VLM process transports resin out of a reservoir on a thin laminate, where it touches the part and is hardened into the next layer. Resin not used in the layer goes back in the reservoir. Pallarés describes the process as “Laminate, transfer, cure, recover resin.” This sequence happens rapidly for each layer. The part itself remains in the open air.
The laminate surface can also move back and forth between resin reservoirs at both ends of its travels, allowing for multi-material builds.
Where viscosity is an impediment to conventional lithography-based 3D printing, the VLM process actually benefits from viscosity, because the resin's viscosity aids in its transfer to the part. The freedom to let the material be viscous expands opportunities for material developers, BCN3D says. Longer polymer chains become accessible. In addition, the viscous resin can carry and support fillers — meaning, for example, use of resins with carbon fiber reinforcement becomes practical. Materials company Arkema has partnered with BCN3D to co-develop materials for the new process.
The material freedom is coupled to what the company sees as freedom to expand the platform to production scale. Every layer requires the same time to cure, whether one part is being printed or 100 at once, the company says. The limitation on parts per build is therefore LCD size. Bigger, cheaper LCD screens will bring faster production rates.
The VLM capability is not yet commercially available. BCN3D says it is seeking users to partner with that can help it to test and further understand the application limits and possibilities of the new process before commercialization comes.
Here is video produced by BCN3D to explain the VLM process:
Related Content
Possibilities From Electroplating 3D Printed Plastic Parts
Adding layers of nickel or copper to 3D printed polymer can impart desired properties such as electrical conductivity, EMI shielding, abrasion resistance and improved strength — approaching and even exceeding 3D printed metal, according to RePliForm.
Read MoreHow to Build 10,000+ Shot Molds in Hours
Rapid tooling isn’t so rapid when it takes days to 3D print a metal mold, and then you still must machine it to reach the necessary tolerances. With Nexa3D’s polymer process you can print a mold in hours that is prototype or production ready and can last for more than 10,000 shots.
Read MoreUnderstanding PEKK and PEEK for 3D Printing: The Cool Parts Show Bonus
Both materials offer properties desirable for medical implants, among other applications. In this bonus episode, hear more from Oxford Performance Materials and Curiteva about how these companies are applying PEKK and PEEK, respectively.
Read MoreAirless Basketball Shows Promise of 3D Printed Lattices: The Cool Parts Show Bonus
Successfully matching the performance of a standard basketball demonstrates the control possible over the mechanical properties of digital materials.
Read MoreRead Next
Looking to Secure the Supply Chain for Castings? Don't Overlook 3D Printed Sand Cores and Molds
Concerns about casting lead times and costs have many OEMs looking to 3D print parts directly in metal. But don’t overlook the advantages of 3D printed sand cores and molds applied for conventional metal casting, says Humtown leader.
Read MoreGE Additive Rebrands as Colibrium Additive
As part of the brand name transition, both the Concept Laser and Arcam EBM legacy brands will be retired.
Read More3D Printing Brings Sustainability, Accessibility to Glass Manufacturing
Australian startup Maple Glass Printing has developed a process for extruding glass into artwork, lab implements and architectural elements. Along the way, the company has also found more efficient ways of recycling this material.
Read More