Binder jetting can be used to print with a variety of powdered materials including metals, sand and ceramics. Binding agent is precisely deposited across the bed of material, joining the particles together to create a “green” form that is typically sintered afterward to form a solid, dense part.
Video: Binder Jet 3D Printing
How Does Binder Jetting Work?
First, a recoating blade or head spreads a thin layer of powder over the machine’s build platform. Next, the printhead (a carriage with inkjet nozzles, similar to those used in desktop 2D printers) precisely jets the binding agent into the powder according to the part’s geometry.
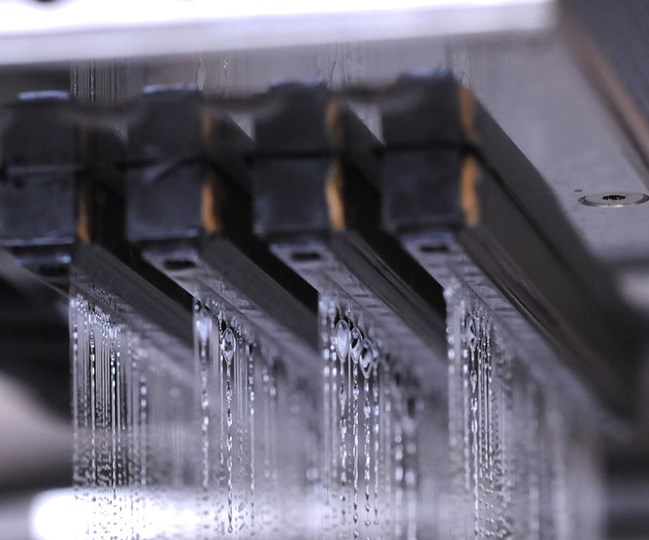
The printhead is a carriage with inkjet nozzles, similar to those used in desktop 2D printers. It deposits the binding agent. Photo credit: ExOne/Desktop Metal
When the binder layer is complete, the build platform lowers, and the recoater spreads a fresh layer of powder across the platform and top of the part being printed. The printhead binds another layer and this process repeats until the build is complete. The entire build envelope is typically cured and/or debound post-printing.
The entire build box is then removed from the machine, parts are extracted and loose powder is brushed or blown away with compressed air in a controlled environment. These green parts may be processed further to impart desired porosity and mechanical properties.
Because binder jetting is performed at room temperature, the process avoids dimensional distortions common to high-heat 3D printing processes, such as warping or curling. If sintering is required, only the bonded powder that forms the parts is subjected to the heat of the furnace, so leftover loose powder can be recycled without fear of degradation.
What Materials Are Compatible with Binder Jetting?
There are a variety of metals available for binder jetting platforms, including stainless steel, nickel and cobalt alloys, copper, aluminum and precious metals.
Ceramics including carbide can be formed into parts via binder jetting as well. Both ceramics and metals require sintering post-printing.
Binder jetting is also used to form parts from sand, typically sand tooling used in metal casting. Sand parts are not sintered post-printing, and are ready to use after loose material has been removed. (Sand prints can also be used for end-use parts as well through techniques that infiltrate the sand with resin to make them more durable.)
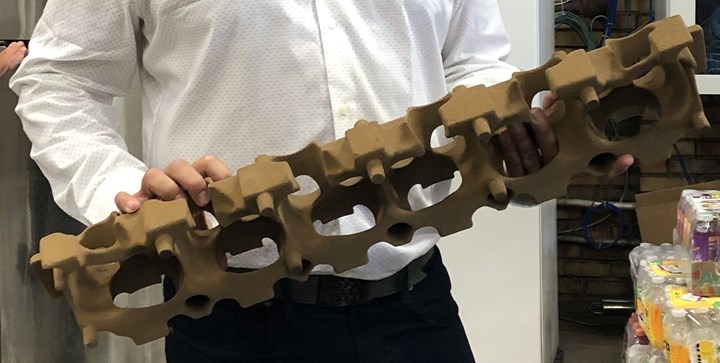
A 3D printed sand core destined for metal casting. Binder jetting allows for a more autonomous method of producing this tooling, without the need for patterns and other hardware beyond the printer.
What Postprocessing Is Required?
Because parts are supported by the powdered material during binder jetting, support removal is not a typical postprocessing step for binder jetting.
Sand cores and cavities produced via binder jetting typically require no additional postprocessing beyond depowdering and are ready to use in their green state.
Metal and ceramic parts require sintering after binder jetting to become fully dense and solid. The sintering process can be conducted in a standalone, enclosed furnace or via a continuous furnace; sintering equipment used for metal injection molding (MIM) is typiclaly compatible with these parts. Sintering causes shrinkage which must be accounted for in the initial part design, and limits the recommended part size.
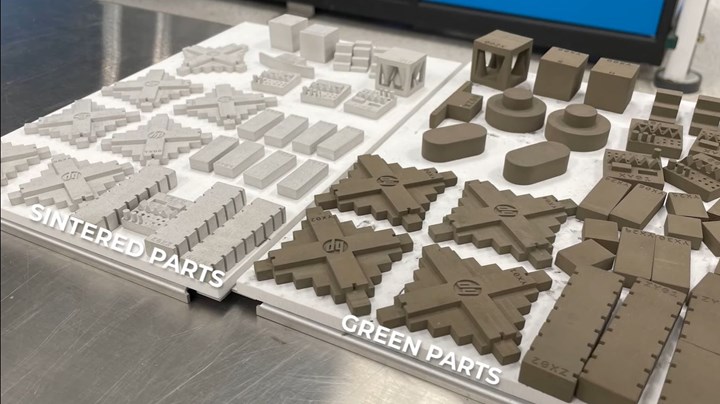
Green binder jet parts (right) experience predictable shrinkage during sintering that must be accounted for during the design process. Sintered parts (left) are dense, strong and ready for end-use applications.
The sintering process results in an average surface roughness fine enough for many end-use parts and features without further processing. Sandblasting and polishing can enhance the surface finish when necessary.
Hot isostatic pressing (HIPing) may be employed to further improve material properties and reduce porosity in solid metals and some ceramics.
Why Use Binder Jetting?
Binder jetting takes place at room temperature and material does not melt in the printer, which means the process can avoid the thermal stresses common to powder bed fusion for metal AM.
Without the influence of heat in the build chamber, unused powder degrades less and is easier to recycle back into the process; material untouched by binder is essentially the same coming out of the build envelope as it was going into the printer.
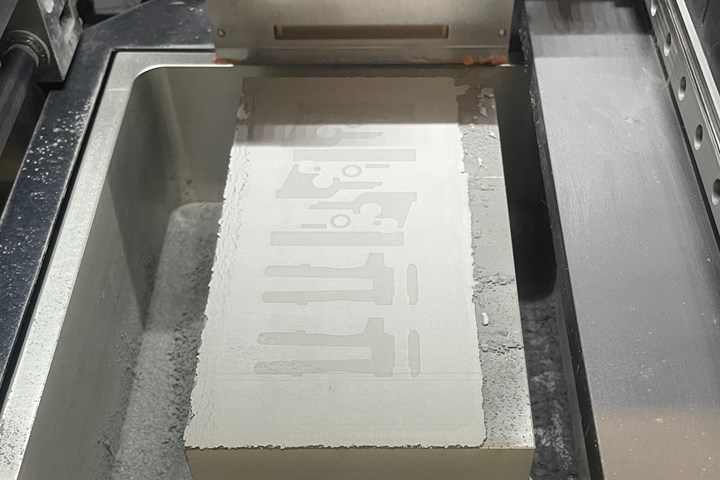
Each layer is created by first spreading powdered material across the bed and then depositing binder to create the layer geometry. Many parts can be nested in a single build for productivity.
The lack of thermal effects means that support structures are typically not necessary. Rather, parts are supported by unused powder and can therefore be stacked in three dimensions, allowing for efficient nesting to produce more parts per run.
The process is an effective way to work with very hard materials that wouldn’t melt easily, such as ceramics, or that would be subject to stress cracking with other processes.
Binder jetting is relatively productive and cost-effective compared to other 3D printing processes. It can run unattended, offering an automated way to produce a range of components with minimal human interference.
What Are the Applications for Binder Jetting?
Copper and stainless steel filters made through binder jetting, created during the coronavirus pandemic in 2020. Photo Credit: ExOne
Binder jetting excels at building smaller metal parts such as industrial components, filters, jewelry, golf club heads, copper windings, shift knobs and automotive engine components. It has also been applied successfully to make tooling for injection and blow molding.
For ceramics, binder jetting offers an easier way to process these materials into functional parts such as silicon carbide nuclear fuel structures, tungsten carbide wear components, nozzles and spare parts. At least one company is also utilizing binder jetted ceramics to produce molds for quick-turn metal casting.
For sand, binder jetting has become an accepted method of producing foundry tooling both for prototyping and production cast parts. Infiltrated sand has also found applications for vacuum- and thermoform tooling and end-use parts such as skate ramps and even PPE.
Related Content
What is Powder Bed Fusion 3D Printing?
Whether in metal or polymer, with a laser or an electron beam, powder bed fusion (PBF) is one of the most widely used 3D printing techniques.
Read MoreAM 101: NanoParticle Jetting (NPJ)
The proprietary process from XJet builds ceramic and metal parts using nanoparticle suspensions. Learn how NPJ works in this introductory article, part of our AM 101 series.
Read More10 Important Developments in Additive Manufacturing Seen at Formnext 2022 (Includes Video)
The leading trade show dedicated to the advance of industrial 3D printing returned to the scale and energy not seen since before the pandemic. More ceramics, fewer supports structures and finding opportunities in wavelengths — these are just some of the AM advances notable at the show this year.
Read MoreA Framework for Qualifying Additively Manufactured Parts
A framework developed by The Barnes Global Advisors illustrates considerations and steps for qualifying additively manufactured parts, using an example familiar to those in AM: the 3D printed bottle opener.
Read MoreRead Next
Understanding HP's Metal Jet: Beyond Part Geometry, Now It's About Modularity, Automation and Scale
Since introducing its metal binder jetting platform at IMTS in 2018, HP has made significant strides to commercialize the technology as a serial production solution. We got an early preview of the just-announced Metal Jet S100.
Read MoreNew Kimura U.S. Metal Casting Plant Relies Entirely on 3D Printing for Molds and Cores
Printing foundry molds and cores without hard tooling will speed leadtimes and make small quantities of castings affordable, the company says. Its proprietary process advances the detail and finish obtainable from casting using sand 3D printing.
Read MoreReusable, 3D Printed Copper Filter: The Cool Parts Show #28
In this episode of The Cool Parts Show, we learn how controlled porosity obtained through binder jetting can be applied to build metal filters capable of trapping — and even eliminating — virus particles.
Read More