The Würth Group, a distributor of industrial supplies, has physical footprints throughout the world that range from large-scale warehouses the company owns and operates down to vending machines placed inside customer facilities. In the past, customers seeking a specific part number from the company would be able to search and select from physical inventory — that is, parts already stored on a shelf somewhere.
But now, Würth customers (and others) will have a second option. At AMUG 2024, the Würth Additive Group (WAG) introduced its Digital Inventory Service (DIS) platform, a service that enables on-demand, localized production of needed parts. Pre-certified parts held in digital inventory can now be securely distributed as digital files through this system, for additive manufacturing at a nearby Würth facility, service provider or right on site. According to a press release issued in March, the DIS builds on Würth’s existing vendor-managed inventory programs and offers customers the chance to create their own full-scale digital inventory solutions.
Würth Additive Group has been developing digital inventory of 3D printable parts for some time, primarily focused on applying the strategy for its own internal clients thus far. Now, with DIS, external companies will also be able to take advantage of the digital inventory using software and tools developed by Würth and customized to their specific needs.
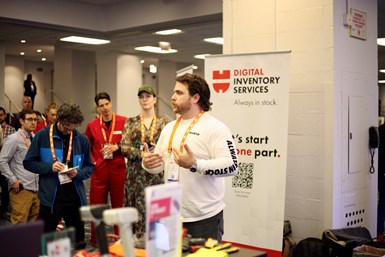
AJ Strandquist, CEO of Würth Additive Group, emphasizes that the Digital Inventory Solution is flexible and customizable to the needs of many users, from large-scale OEMs to individual autobody shops. Source: Würth Additive Group
“We’re used to meeting the different requirements that OEMs have,” says AJ Strandquist, CEO, Würth Additive Group, stressing the adaptability of the solution. “We’re building the plumbing — the infrastructure — to let them have the solution they want.”
DIS is process, machine and file type agnostic, as well as fully customizable to the requirements of the user. Early pilot customers represent a range of possible use cases and the diverse needs that the platform can be customized to support: a large OEM applying DIS as an internal solution for tracking and controlling tooling 3D printed by a central additive team; an automotive OEM that is tapping Würth capacity to produce on-demand parts; and an autobody collision shop that orders aftermarket parts through its local Würth branch and pays royalties to manufacture them on its in-house 3D printer.
How the Digital Inventory Solution Works
The Digital Inventory Solution integrates with Würth’s existing vendor-managed inventory programs, systems and software; many tool crib managers, mechanics and other users will order digital parts through their existing parts portals. Source: Würth Additive Group
DIS is multifaceted, consisting of both software — which enables the secure storing and sending of part files and manufacturing information — and hardware, specifically an Internet of Things (IoT) “edge” computing device that can be linked to 3D printers that will be used for manufacturing. It also requires data about digital inventory parts: machine, material, build setup, postprocessing and quality assurance as specified by the OEM, so that a qualified part can be reproduced at a moment’s notice.
The job overview for a DIS part includes information about the required printer, material and authorized quantity. Source: Würth Additive Group
I got an early demonstration of the DIS platform in December 2023 via a Microsoft Teams call with WAG team members located across two continents. WAG technology leader Mikhail Gladkikh, sitting in Houston, Texas, used the DIS to securely send an encrypted build file to Philipp Weimann (product owner at Generic.de Software Technologies AG) in Germany. Within seconds, the build file was delivered directly to a 3D printer at the Europe location (users have no access to the design or setup files, to avoid any risk of alterations) via the edge device, which decrypted the data
3D printing is only one step in the additive manufacturing workflow, however, and data communicated to the 3D printer can only go so far — and so the DIS also includes support for the human aspects of the process in the form of text-based instructions to ensure digital inventory parts are not only printed, but fully manufactured to spec.
The DIS platform supports a full “recipe” to ensure repeatable manufacturing of digital inventory parts, including detailed postprocessing instructions.
Source: Würth Additive Group
“It’s really a ‘recipe’ for every part,” Strandquist says.
This “recipe” documentation is customizable to the user’s requirements, and can include a list of required equipment, including PPE, printer, material and any postprocessing implements, as well as guided steps for postprocessing and quality control, prompting the operator to confirm compliance at every step.
The system is flexible enough to allow for different skill levels (OEMs can load both quick-start-style guides and more detailed step-by-step instructions for operator reference) and the varying requirements of diverse additive applications. A part intended for internal plant use like a hand tool might have minimal requirements beyond removal from the build plate and a quick vision check, while a component for automotive repair might require more cleaning, postprocessing and quality checks such as dimensional measurements, mechanical tests or even scan data.
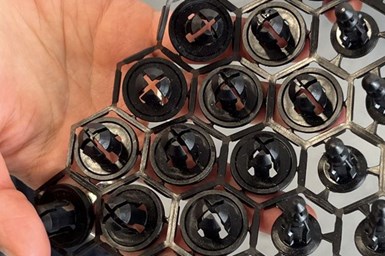
One DIS pilot user is an autobody shop currently applying the system to manufacture repair items like clips on-site. The shop orders clips from their local Würth supplier as usual, pays a royalty fee, and then receives the encrypted files to produce the items on its own 3D printer.
Files are licensed products and the number of times a part can be printed is controlled; while many applications for DIS are likely to be internal at first, this opens the door for OEMs to distribute production of spare or replacement parts to service providers, while maintaining IP control and capturing revenue.
“Today many aftermarket automotive parts are produced by third parties, for example,” Strandquist says. “Now OEMs can put out a validated part file for those third-party manufacturers or even shops to use through DIS. They can retain more control over aftermarket parts and capture royalties from those transactions.”
“Always in Stock”
Over the coming months, WAG will be educating Würth sales representatives in 26 countries on the value proposition from 3D printing and digital inventory. These representatives will become champions of the solution that can present its benefits to existing and new Würth customers. The group will also be collaborating with 3D printer OEMs to expand support for the DIS platform, bringing new customers on board, and sharing successes from the pilot users.
Digital inventory may not be a solution for keeping every part in stock, yet for those that can be digitized, the impact can be significant. Manufacturers and other users can stay responsive, without having to depend on physical inventory availability or being subject to long lead times for parts that aren’t in stock. OEMs can securely distribute products, enabling faster service and potentially new streams of revenue. Manufacturing distributed through such a platform also reduces shipping and the associated CO2 emissions from moving parts, as well as the impact of packaging and raw materials.
“If you can ship 10 raw materials across a border to be made into digital inventory parts, you can get rid of all those tariff codes for what might be thousands of items,” Strandquist says.
The logistics become simpler, in addition to the ecosystem impacts of moving parts and materials — particularly in emergency situations such as a warranty event when many parts might be needed in many locations quickly. DIS can enable a rapid, efficient response, even if it isn’t the everyday solution for delivering the service parts.
“It’s hard to calculate just how inefficient the supply chain is when it breaks,” Strandquist says. “This is one more tool on top of our other inventory management solutions to always keep people’s parts, tools, fixtures — whatever their factory floor needs — in stock.”
Related Content
MC Machinery’s Wire-Laser Metal 3D Printer for Efficient, Versatile Processing
The printer applications include rapid prototyping, mold and die, one-offs, short runs, mass manufacturing, maintenance, repair, tooling and more.
Read MoreLincoln Electric Helps Get Chevron Refinery Back Online
Lincoln Electric worked with Chevron to accelerate refinery maintenance using Lincoln Electric’s 3D metal printing solution.
Read MoreHow a DOD-Funded Resilient Manufacturing Ecosystem (RME) Is Coming Together at Neighborhood 91
Pittsburgh’s additive manufacturing campus doubles as a test bed for a Department of Defense project aimed at developing a reproducible ecosystem for on-demand production of critical parts.
Read MoreRoss Develops Customized, Fully Enclosed Mixing/Melting System
The system features a specially designed elevator system which enables the mixers to be lowered to a maintenance position and raised to an operating height, thereby enabling gravity to feed from the melter into the holding tank.
Read MoreRead Next
Do Distributors Dream of Digital Inventory? Würth Additive Group Does
It’s more than a dream for Würth Additive Group and its parent company, in fact. Along with supplying additive equipment, the group is now developing solutions for sourcing 3D printed parts in a reliable, elastic digital inventory model.
Read MoreIs a Functional 3D Printer Network Possible? Automation Alley’s Project DIAMOnD and the Industry 4.0 Future
The initiative that placed 3D printers at more than 300 Michigan manufacturers is laying the groundwork for a future in manufacturing that is digital, distributed and largely additive.
Read More3D Printing for Supply Chain Resiliency: AM Radio #39
Additive manufacturing can speed, strengthen and simplify industrial supply chains. How close are we to realizing this promise? Dr. Tim Simpson and Peter Zelinski discuss lead time, logistics and other factors on AM Radio.
Read More