While additive manufacturing (AM) is often thought of as disrupting production by offering an alternative to conventional manufacturing processes, it can also be an aid to conventional manufacturing. AM can offer a better way to make tooling, which in turn amplifies conventional manufacturing processes. In fact, tooling may be additive manufacturing's most impactful application.
In this context, tooling is any part manufacturers use to make other parts. It could directly form the part—as in a mold or layup form—or it could be a step removed, like a pattern for a mold that manufacturers would then use to cast a different part. It could even be something that comes along later in the manufacturing process, like jigs, fixtures or assembly tooling.
Despite production-additive manufacturing being the most visible form of AM technology, tooling is the mechanism that typically introduces AM into the production chain at machine shops. Many companies are using polymer 3D printing to aid other processes, with 10 particularly clever AM applications listed below.
1. Sharonville Transmission Plant: Pucks and Workholding Fingers
The Sharonville Transmission Plant located just outside of Cincinnati, Ohio has finished and assembled transmissions and gears since around the late 1950s, and employs about 1,600 workers today. Plant employees Jonné Messer and Jeff Fisher report that sections of the plant shut down every day when parts of different assembly lines break.

This first image shows one of the parts that breaks consistently: the pucks that drive along the rails that carry parts down the line. There are nine of these lines in the plant, with 67 pucks on each line. Each puck costs $180 to replace through traditional manufacturing methods. Jonné and Jeff convinced management to buy a modest FDM printer and take a few classes on how to use it, and the two soon replaced every single puck at the plant with a 3D printed one for a total material cost of $330. In 2020 alone, the plant says it has saved over $100,000 by 3D printing them in-house.
Another replacement part includes a workholding device that allows a robot to grab the outer rings, which are then bolted to a pallet that travels down a conveyor. When these fingers were made of metal, they nicked and scratched the rings — a problem that cost the company more than $1 million per year. Now the plant 3D prints them out of PET G in different colors for different sized rings, and the nicking and scratching issue has gone away completely.
2. Fortify: Ventilator Part Mold
3D printing for mold tooling typically typically involves a metal tool in which conformal cooling channels have been printed to help the mold cool faster, resulting in higher turnover and productivity. That's a great use case, but this next example is different.

The white part shown here is an adapter that converts a CPAP machine into a substitute ventilator. This was a project from an organization called Ventilator Project that was attempting to help healthcare workers source ventilators at the start of the COVID-19 pandemic. Ventilator Project, which was working on an accelerated timeline and trying to decide between two designs, priced out conventional metal tooling and learned it would cost thousands of dollars to test even a single design.
Ventilator Project decided to collaborate with Fortify, a company in the Boston area that specializes in 3D printing polymer composite injection mold tools. Together, they were able to 3D print both the mold cavity and the two orange pieces shown in the image. These are two different sets of the cores that would allow Fortify to rapidly test both designs. The tooling only cost about $700, with a lead time of about a week.
As a result, Fortify was able to mold prototypes on this tooling and then do a short production run from its facility. This was an instance where the 3D printed tool was not meant for the full production run, but the intermediary step between prototyping and production to quickly produce a design, in this case for FDA validation. It worked so well, though, that Ventilator Project began producing parts while waiting on more conventional tooling. Read more in the linked article.
3. Precision Metal Products: Custom Workholding Solutions

This workholding example is from a machine shop called Precision Metal Products based out of Milford, Connecticut. The company traditionally takes on high-volume contracts, which places a premium on throughput and spindle uptime. The bottleneck they routinely encounter centers around the labor-intensive, expensive, time-consuming process of creating custom workholding devices. Many of these take more than a week to manufacture, all for typically one-off parts. While the company creates plenty of commonplace examples of 3D printed workholding tools, the box shown in this image is something more unique.
One of the parts the company produced was a 17-4 stainless steel medical device that measures less than a tenth of an inch in diameter. The tooling for the workpiece was only a quarter-inch in diameter, and creating that tooling involved two or more setups, CNC programming, special fixturing and wire EDM. But the problem that was routinely encountered during the CNC machining process came from the force of the coolant, which would blast the part out of the vise and into the back of the machine. When the designers redesigned the tooling for 3D printing, they created an open-ended box with walls that include hundreds of small triangles — essentially a five-sided screen that allows the coolant to flow through. They also included a half-inch hole located in the middle of the box that the workpiece snaps into vertically, allowing the spindle to access all sides of the part within the confines of the box.
To keep the box itself secure, the designers printed four encasements in each lower corner that each housed a magnet that helped secure the box to the metal vise. As machining took place and as each part was cut free from the stock, the parts fell into the box and attached themselves to one of the four magnets in the corners as the coolant evacuated through the flood slots.
[Related: Another machine shop success with 3D printing for workholding]
4. Guhring: Cutting Tool

Maybe the most fundamental type of tool in a machine shop is the cutting tool, and metal 3D printing is seeing more and more use to make cutting tools. This tool is from cutting tool maker Guhring, and was printed on a Markforged Metal X additive manufacturing machine.
Importantly, the cutting edges were brazed on rather than 3D printed. But the fact that entire tool body was 3D printed allowed Guhring to incorporate channels for the cutting fluid to flow through the tool and out near the cutting edge in exactly the placement they needed. For more information, check out The Cool Parts Show’s season 3 premiere, which focused on this tool.
[Related: Another, much bigger 3D printed cutting tool]
5. Lincoln Electric Additive Solutions: Aerospace Facesheets
Lincoln Electric Additive Solutions is a relatively new division of Lincoln Electric, the 125-year-old year old global manufacturer of welding equipment. This new division specializes in large-scale robotic metal 3D printing, also known as wire arc additive manufacturing, a process that combines automated MIG welding or laser hot wire welding with direct-deposition 3D printing. Essentially, it involves an industrial robot arm fitted with a welding torch depositing bead layers of melted wire feedstock onto a multi-axis turntable.

A prime use case for this is aerospace tooling for composites, including the tool shown here called a facesheet. Facesheets are large, asymmetrical tools that can take months to manufacture, not only because of the availability of raw materials such as Invar, but also because facesheet tools require significant amounts of time to fabricate and machine on CNC machines large enough to handle them.
While 3D printing these parts via wire arc AM is still not an easy process — the printing process takes eight days, and the finished product is so large that Lincoln Electric needed to purchase a company that could finish machine the parts on massive five-axis machining centers — this process still literally shaves months off the lead time for producing these parts via traditional manufacturing processes. Read much more about wire arc additive manufacturing.
6. Humtown Additive: Foundry Water Jacket Mold Core
Many molds and cores used for foundry tooling are made of sand. One conventional process for building these tools is to make a pattern, pack the foundry sand around it, burn out the pattern, cast the metal, then destroy the sand mold to remove the part.

This example shown here comes from Humtown Additive, a sand 3D printing facility based near Youngstown, Ohio. The company uses large-format binder jetting systems that adhere the sand together to form mold cores for what will eventually become tooling. The tool shown here casts the water jacket for an engine block — a tool the company used to produce by blowing foundry sand into another mold. Using the conventional process, the company couldn't maintain the quality of the sand throughout the core, a problem that produced a spongy quality in the middle of the part. This resulted in several failures and a high scrap rate on these parts when the foundry would try to cast them.
Humtown Additive discovered it could 3D print this core to maintain the quality throughout this entire complex geometry, resulting in higher quality castings. In this case, 3D printing allowed for assembly consolidation and the geometric complexity typical of production parts, but in this case applied to tooling to achieve a better end-use part.
Another interesting point with this story is that the core is actually the only 3D printed tooling Humtown Additive uses. The company kept the rest of the mold conventional to reduce costs, showing that additive manufacturing not an all-or-nothing proposition. Companies can 3D print part of the tool, instead of the whole thing. In fact, there can be really good reasons to use both processes in tandem like this. Read more about the role and application of sand 3D printing.
7. Exco Engineering: Die-Making Water Jackets

Exco Engineering, located near Ontario, Canada, is a die maker for the automotive industry that 3D prints inserts for engine block dies, including the water jacket in the image.
If you think of the engine block die as a large negative space of an engine block, the water jacket is an insert that forms a figure-eight cooling channels filled with water, like a jacket around cylinder bores. The image shows a demo version of a 3D printed water jacket that is opened up to display the cooling channels inside. The superior cooling of this type of water jacket prevents the buildup of solder, which can increase cycle time for polishing as well as cause part fatigue, cracking and failure. These water jackets wear out so frequently that these engine block die casting tool components are basically production parts to Exco.
8. Thyssenkrupp Bilstein: Cobot Grippers, Spacers and End Effectors
Sticking with automotive, the image below shows collaborative robots, or cobots, in use at Thyssenkrupp Bilstein’s main North American production facility located near Cincinnati, Ohio. Bilstein is perhaps the premier suspension supplier for the performance and luxury auto market, and it has integrated these cobots into its production processes, typically for handling metal tubes during different stage of production.
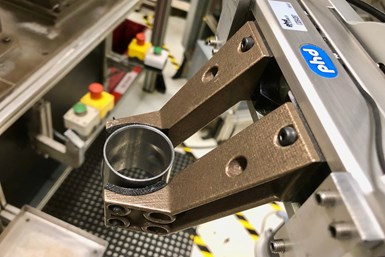
A few years ago, Bilstein realized it was spending a lot of money replacing the cobot grippers, spacers and end effectors, which can each cost more than $800 to replace. To lower costs, Bilstein purchased a handful of Raise3D printers and began printing these components with PLA and TPU, at a cost of less than $5 worth of material. Some of the grippers have been in use on the cobots for more than a year, showcasing the durability of PLA and TPU materials.
9. PMT Shielding Solutions: Custom Masking Tooling
Like water jackets at Exco, this application uses so much tooling that the tools themselves are basically production parts. PMT Shielding Solutions in Tigard, Oregon, plays an important role in the production of electronics products, applying a metal coating for shielding to the plastic parts used in electronics.

The big cylinder in the image shown here gets wheeled into a vacuum chamber for coating, including all of the small pieces that surround it. Each one of those parts needs a custom tool to make sure the coating lands in the right place. 3D printing has proven to be the most way for PMT to make this tooling. Its 3D printers from Plural Additive Manufacturing basically run around the clock to create custom masking tooling tailored to the parts PMT will be coating with metal.
10. Gate Precast: Forms for Precast Concrete Panels
This example showcases Gate Precast, a precast concrete manufacturer in Winchester, Kentucky. While concrete may not seem like a manufacturing topic, it actually shares a lot of commonalities with composites.

In this example, Gate Precast was tasked with creating all of the precast windows for a skyscraper in New York City on the site of the old Domino sugar manufacturing facility. Naturally, the builders wanted a facade that would reflect that history and resemble a sugar cube. To do so, Gate Precast created around 1,500 precast concrete panels of three windows each.

If the company had done this conventionally, it would have needed to build all of those forms out of plywood, as shown in the foreground of this second image. Of course, this is a time-consuming, labor-intensive process, and those plywood forms last only for 10 to 20 concrete pours. That life expectancy is fine for renovating a smaller building or for a small order, but the cost and time to make all the tooling is unfeasible for a building with 47 stories.
To solve this problem, Gate Precast began working with Oak Ridge National Labs, Additive Engineering Solutions (AES) in Akron and Thermwood in Indiana, to 3D print these forms on large-scale additive manufacturing machines, specifically the LSAM from Thermwood and the BAAM machine from Cincinnati Inc. The black forms in the background of the second image are the 3D printed forms, which were ABS reinforced with chopped carbon fiber. While the printed forms were actually much heavier than the wooden forms, they were far more durable and much faster to produce. Some of these forms were used up to 200 times in the course of the project and were still usable when production finished.
By using 3D printing, Gate Precast was able to save the time, labor and materials it would have taken to build the forms in their carpentry shop, ending up with something much more durable.
In short, tooling is a big win for additive manufacturing — maybe the big win. Most facilities could likely produce their tooling more effectively through additive manufacturing, and getting good at additive manufacturing by using it for tooling might very well be the step that gets organizations ready for 3D printing for full production.
Related Content
What Does AM Want? Here Are 4 Aims (Maybe 5) That Additive Manufacturing Is Driving Toward
Certain freedoms and contributing factors allow additive manufacturing to realize its full promise for production.
Read MoreFrom Parts to Problem-Solving: 3DEO's Evolution with Intelligent Layering Metal 3D Printing
The technology developer and parts provider is moving beyond transactional 3D printing, in favor of holistic solutions where its AM process can have the greatest impact.
Read More8 Cool Parts From Formnext 2023: The Cool Parts Show #65
New additive manufacturing technologies on display at Formnext were in many cases producing notable end-use components. Here are some of the coolest parts we found at this year’s show.
Read MoreCreating Designs That 3D Printing Experts Love
3D printing can create virtually any shape imaginable, but that doesn’t mean it will be easy to print. How to design parts that are printable as well as functional.
Read MoreRead Next
The Hidden Complexities of Wire Arc Additive Manufacturing
Lincoln Electric Additive Solutions’ robotic metal 3D printing process is a choreographed dance between welding, robots, automation, heat management and machining. The new venture may have a distinct advantage in the field: its parent company’s 125 year-old legacy.
Read More3D Printed Tool for CNC Machining: The Cool Parts Show #17
Guhring uses additive manufacturing to make an end mill with optimized internal channels. We visit a machine shop to test the tool on this episode of The Cool Parts Show.
Read More3D-Printed Molds Accelerate Substitute-Ventilator Validation
Fortify’s 3D printing and injection molding expertise saved Ventilator Project weeks and thousands of dollars as the nonprofit hurried to supply clinicians and hospitals at the start of the COVID-19 pandemic.
Read More