3D printed polymer makes complexity accessible (if not entirely “free”) but there are applications where polymer alone is not sufficient, and printed metal is out of reach for timeline or budgetary reasons. In these cases, electroplating may be an option — using a series of chemical baths to apply layers of metal, usually nickel or copper, to a part’s outer surface to enhance its appearance or properties.
The effect of plating can be purely aesthetic, but for RePliForm, electroplating goes more than skin deep. For years this Baltimore-area company has specialized in electroplating of plastic parts, specifically those produced through 3D printing. The reasons for plating vary but the company’s work is largely focused on adding functionality.
Electroplating can be used to make polymer parts conductive, capable of EMI shielding, resistant to abrasives, and perhaps most significantly, much stronger than polymer alone — and often comparable to 3D printed metal. (Sean Wise, president, refers to this reinforcing capability as “structural electroplating.”) Regardless of the reason, the company’s work effectively offers the chance to combine the geometric possibilities of polymer 3D printing with material properties of metals, reducing costs while providing an option in between either material alone.
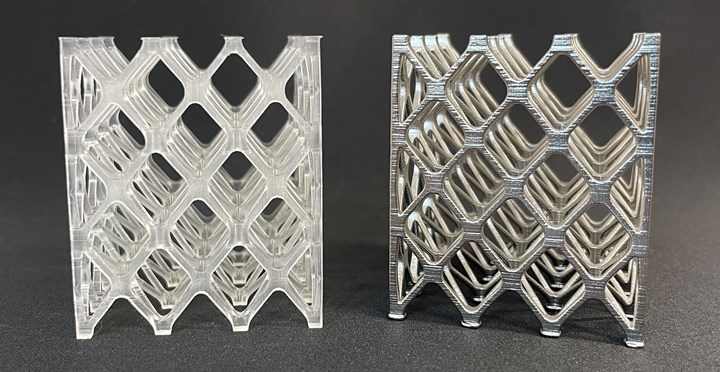
These lattice cubes were 3D printed from clear resin using stereolithography, then coated with electroless nickel, copper, and layers of ductile and hard nickel to improve their compression performance. See the process and view testing results.
A 3D Printed Foundation
RePliForm began as a provider of services for electroforming, from which it derives its name. The electroforming process uses electrical currents applied within a tank to form sheet metal around tools such as molds or patterns. That need for tooling is how RePliForm first got acquainted with 3D printing, adding an SLA printer to produce the forms for shaping these parts.
“Essentially, we stopped removing the forms,” Wise says, describing RePliForm’s eventual pivot into plating.
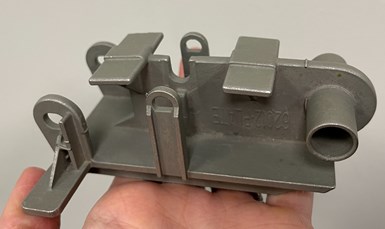
This reversing arm assembly produced for Pitney Bowes in 2003 was created by plating an SLA 3D printed component with 50-75 microns of copper and nickel. The plated polymer part survived 400,000 cycles for testing without failure, and changed the course of RePliForm’s business.
There was one job in particular that changed the course of the business back in 2003. Mailing equipment OEM Pitney Bowes needed functional versions of a reversing arm for a mail sorting machine for testing. The final part was designed to be injection molded from carbon fiber reinforced polycarbonate with Teflon particulate filler, and the company wanted to avoid the cost and time of making a prototype tool to mold test parts. However, creating a prototype part that could survive the 400,000 cycles proved difficult. The best SLA resins at the time lacked the stiffness and strength needed, Wise says, and would often creep out of shape; at best, parts made this way could be expected to last only around 20,000 cycles in the machines.
The team at Pitney Bowes came up with the idea to use electroplating to reinforce the SLA prints, and offset the part surfaces to make room for the coating before sending them to RePliForm for this step. Plating the prototypes with 50 to 75 microns of copper and nickel increased their durability to the point that Pitney Bowes was able to reliably achieve 400,000 test cycles on the machines without failures. Printing and plating took just 1 week, Wise recalls, and was around 10% the cost of building prototype tooling and molding parts.
“This part defined the direction of our business,” Wise says. “We realized this was a product other people could use. We could offer an intermediate option between metals and plastics.”
Today RePliForm applies its electroplating expertise almost exclusively to 3D printed polymer parts, adding layers of nickel and copper to achieve whatever requirements the customer has. Electroplating uses some of the same principles as electroforming, but rather than forming a piece of solid metal around a pattern that will later be removed, plating builds a coating directly on the part’s surface. The process transfers material from corroding metal anodes to a part that’s been made conductive so that it can act as a cathode inside an electrolyte bath.
The thickness of the resulting layer is a function of time, bath chemistry and temperature, electrical current, and the geometry of the part. (And because electroplating takes place in an aqueous bath running at low temperatures — less than 45°C — it’s compatible with most printable resins.)
Preparing 3D Printed Polymer Parts for Electroplating
Electroplating is a well-established and industrialized process, but plating on printed polymer parts poses some unique challenges. Parts must be clean, watertight and conductive for successful electroplating, and preparing them for this process is a significant proportion of the work involved.
“We need to understand all the things that happen to a part before it gets here,” Wise says, because design, material, print process and postprocessing all have impacts on the plating workflow needed.
Electroplating adds layers of material, so parts should be designed to accommodate this as well as to allow for access to all the features that need plating. There are no prescriptive recommendations for material and process, but both of these are important to know in advance. The most common types of 3D printed parts that RePliForm sees are made through photopolymerization, selective laser sintering (SLS), Multi Jet Fusion (MJF) and fused filament fabrication (FFF), and could be a variety of materials including nylon 11 and 12, ABS, Ultem, or polycarbonate. The substrate material will determine the plating workflow, while the 3D printing methodology and any postprocessing steps provide clues as to the incoming surface quality and porosity of the workpiece.
Thermoplastic 3D prints for example tend to be porous, which can draw in the plating electrolytes and cause defects in the finish. Parts made through FFF are generally not watertight and need to be sealed before plating, typically with epoxy but vapor smoothing can also be an option for some parts. Others can be made watertight during the printing process; SLS parts, for instance, can be built by applying more energy on the outer surface during printing to create nonporous walls. A few 3D printing techniques like photopolymerization and STEP from Evolve Additive Solutions produce watertight parts that require no further sealing.
Clean and watertight parts are mechanically etched with a fine abrasive when they arrive at RePliForm to encourage adhesion. Then the polymer parts go through a room-temperature electroless nickel line, a process that applies a thin coat of nickel phosphorus to the plastic surfaces to make them conductive, enabling the workpieces to act as cathodes in the electroplating step.
Finally, parts go through a series of copper and/or nickel baths to build up the needed layers of functional material through electroplating.
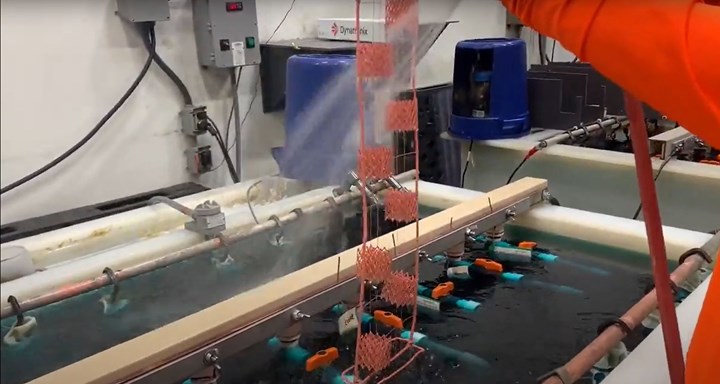
Following the electroless nickel process, most parts are first plated with copper even if they will go on to be electroplated with nickel, like these compression cubes. RePliForm’s capabilities include “self-leveling copper,” a technique that can smooth surface defects before subsequent plating steps. Photo Credit: RePliForm screenshot
Parts are plated based on their application — where some customers are only interested in aesthetics, many more are interested in improving the hardness, strength, conductivity or other properties of their parts. The work is about 50% prototyping and 50% production parts, and tends to come in small batches.
“We’re not focused on volume,” Wise says, emphasizing the company’s flexible tank setup that makes it easy to change out the workflow at a moment’s notice.
Applications for Electroplated Polymers
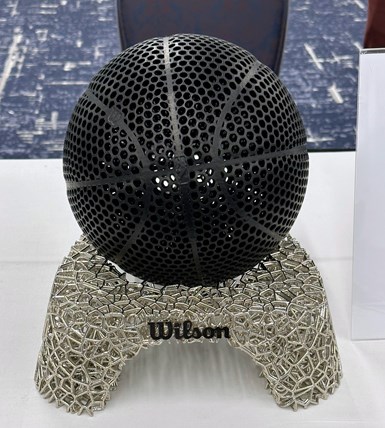
Wilson’s airless basketball prototype was created through collaboration with General Lattice (which provided design expertise), EOS (which performed the selective laser sintering) and DyeMansion (which vapor smoothed and dyed the part). The stand used to display the ball was also 3D printed by EOS and smoothed by DyeMansion before RePliForm electroplated it. Photo Credit: RePliForm
While much of RePliForm’s work is proprietary, some public projects offer illustrations of the value of electroplating for 3D printed polymer. In addition to offering an option between metal and plastic, plating can be fast — fast enough to justify this approach versus a direct metal print where that may not be possible. In one recent high-profile case, RePliForm was asked to electroplate two stands for the Wilson airless basketball prototype, developed in partnership with General Lattice, EOS and DyeMansion. It received the vapor-smoothed SLS prints on a Friday, and by Monday had finished, plated parts.
EMI shielding applications, where conductive materials are applied to reduce or block electromagnetic fields, are the company’s bread and butter at the moment; just 50 microns total of copper (which provides the shielding functionality) and nickel (which prevents oxidation) is enough for most high-frequency EMI applications, meaning the rest of the structure can be low-cost, lightweight polymer.
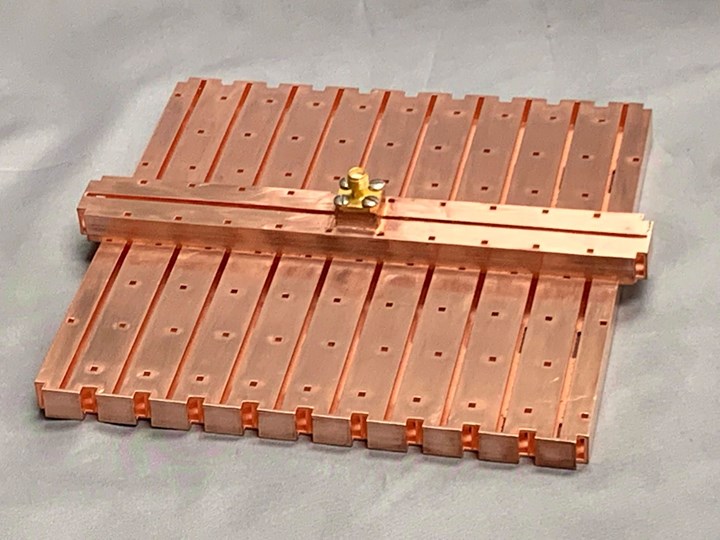
This waveguide slot array antenna produced by plating an SLA print with copper represents significant time, cost and labor savings to produce a device like this. More in this article from IEEE. Photo Credit: RePliForm
Antennas are another significant application; this waveguide slot array antenna (above; also seen at RAPID 2022) is an example. Components like this are typically made from brazed and soldered copper. Here, the waveguide designer had already been exploring 3D printing these devices and was in the process of adding perforations to the geometry when he began collaborating with RePliForm. Wise asked the designer to remove as much material as possible without affecting the waveguide’s performance, which ultimately allowed for the necessary access to clean, etch and plate this part. Applying a layer of about 50.8 microns of copper made the polymer print into a functional antenna, with fewer steps than a conventional manufacturing process. The part was produced in just a few weeks, offering identical performance while also being lighter weight than an assembled copper device.
Structural components continue to be of particular interest. Ultimately, Wise sees significant opportunity for plated polymer parts to fill the gap between straight 3D printed polymer and 3D printed metal.
RePliForm has found that electroplated polymer fills a niche between pure plastic and pure metal 3D printed parts in terms of properties including tensile strength and tensile modulus. Click to expand. Image Credit: RePliForm and Formlabs
“We look at plated polymer parts as a composite,” he says. In fact, RePliForm has applied the rule of mixtures, a basic formula of composites, to predict tensile strength of plated parts based on the volume fraction and properties of the constituent plastic substrate and metal coating. Generally, the higher the volume of metal in the final part, the stronger it will be. Stiffer starting resins reinforce better, though soft materials will begin to converge with these properties at higher volumes of metal.
“Above 20% metal, the base material has less of an impact,” Wise says. Most of the reinforcing work the company has done operates at a lower percentage than this, but there has been experimentation to push this strategy to its limits.
These topology optimized beams were designed by nTop, 3D printed using Formlabs SLA printers, electroplated by RePliForm and tested at Penn State University. Study results.
In one case study conducted with Penn State University, nTop and Formlabs, a plated polymer part actually out-performed a 3D printed metal one. A beam designed and optimized by nTop was 3D printed on a Formlabs SLA printer and plated with nickel in successively higher volumes.
“We chose a plating sequence and thickness where the rule of mixtures indicated that we should get similar tensile strength to DMLS aluminum,” Wise says. This prediction was verified in testing standard ASTM D638 tensile specimens made from electroplated SLA samples.
Testing of the topology optimized beams compared plain 3D printed resin, versions electroplated with ductile and hard nickel, and aluminum parts 3D printed directly through laser powder bed fusion. The hard nickel version outperformed other parts in terms of load deflection, max load and several other metrics. Image Credit: RePliForm
In tests of the printed and plated topology optimized beams, the version with the highest metal volume (34% metal consisting of 10% copper and 90% nickel) actually outperformed a direct 3D printed aluminum version in terms of strength, achieving nearly twice the latter part’s maximum load. According to Wise, the stronger-than-expected strength was likely related to the type of failure (bending and buckling, with the loads highest at the surface — precisely where the metal plating is).
“It turned out to be an ideal candidate since the loads are borne on the outer surfaces,” he says. “We tend to get more plating on these outside surfaces and the ligaments, which is what failed, enhancing the effectiveness of a strong surface coat versus the monolithic DMLS aluminum piece.”
For now, realizing results like this depends mostly on trial-and-error and past expertise. Plating on 3D printed parts has not been well studied, and software for simulating resulting process and material properties does not exist. Such a solution would need to include some combination of generative design and stress analysis software, and ideally incorporate electroplating field analysis to look at plating distribution as well.
“We need to better understand DFAM [design for additive manufacturing] for these two-phase parts,” Wise says, “to exploit the plating and all the variables. We need to get to the point of modeling plating itself.”
RePliForm is open to collaboration on the design and simulation front. But in the meantime, the company is pushing the envelope and attempting to learn as much as possible about the capabilities and limitations of plated 3D printed parts through practical applications.
“The thing about plating,” Wise says, “is that it can do a lot of things at once.”
Related Content
How to Improve Polymer AM Productivity 20X
A fast cycle time is critical to efficient production 3D printing, but it’s not the only thing. How you choose the right parts for AM, prepare jobs for production, and manage post processing will have just as big an impact on total 3D printing throughput. It all needs to work together to achieve maximum productivity.
Read MoreAM 101: Digital Light Synthesis (DLS)
Digital Light Synthesis (DLS) is the name for Carbon's resin-based 3D printing process. How it works and how it differs from stereolithography.
Read MoreHow Large-Format 3D Printing Supports Micro-Scale Hydropower
There is potential hydroelectric power that has never been unlocked because of the difficulty in capturing it. At Cadens, additive manufacturing is the key to customizing micro-scale water turbine systems to generate electricity from smaller dams and waterways.
Read MoreDrones Take Flight with Metal and Polymer 3D Printed Parts: The Cool Parts Show Bonus
Drones produced by Cobra Aero now incorporate many 3D printed parts made through laser powder bed fusion and Multi Jet Fusion processes.
Read MoreRead Next
A Conversation on Finishing's Role in Additive Manufacturing: AM Radio #12
Conventional finishing techniques like electroplating and powder coating have a role to play in AM. Stephanie Hendrixson and Scott Francis discuss how additive will go farther with finishing on the latest episode of AM Radio.
Read MoreHybrid Additive Manufacturing Machine Tools Continue to Make Gains (Includes Video)
The hybrid machine tool is an idea that continues to advance. Two important developments of recent years expand the possibilities for this platform.
Read More4 Ways the Education and Training Challenge Is Different for Additive Manufacturing
The advance of additive manufacturing means we need more professionals educated in AM technology.
Read More