ABB Introduces Software Capabilities to Simplify Robot Programming for AM (Includes Video)
Slicer software output can be converted to a robot program. The user chooses speed and precision of printing, but no specialized knowledge of robot 3D printing is needed.
Robots are ready to serve as fast and capable industrial 3D printers, but they are not necessarily easy to program for this application. Robot maker ABB has addressed this challenge with new 3D printing capabilities added to its simulation and programming software, RobotStudio, allowing the output of any third-party 3D printing slicer software to be converted automatically into a program for robot motion. No special knowledge of robot programming for 3D printing is required, the company says.
Robots are a natural fit for 3D printing. The programmable motion control of an industrial robot is easily precise enough for material-deposition 3D printing, while the long reach of a robot provides an option for large-format AM that is potentially more economical than a large, dedicated 3D printer necessitating a large enclosed machine frame.
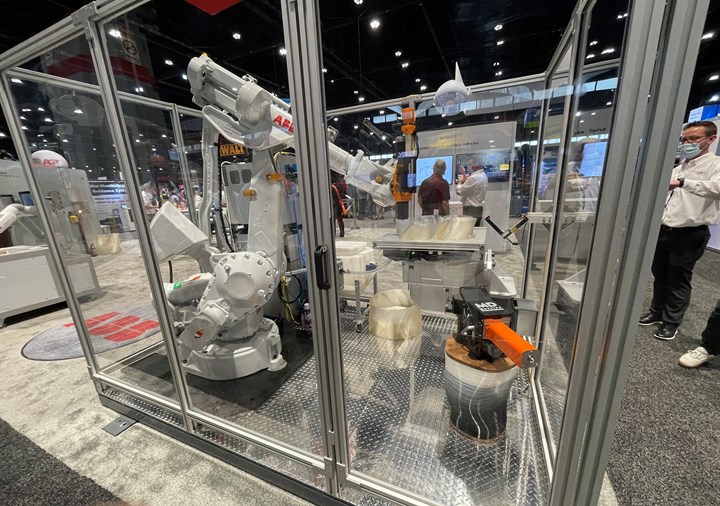
In fact, other hardware to enable robotic 3D printing is ready to go as well. Extruders engineered for 3D printing provide an effective means of depositing material with a robot. Programming has presented the most significant remaining barrier to making use of these resources. In ABB’s case, programming a robot for 3D printing has, until now, generally required a third-party software tool combined with specialized robot programming skill.
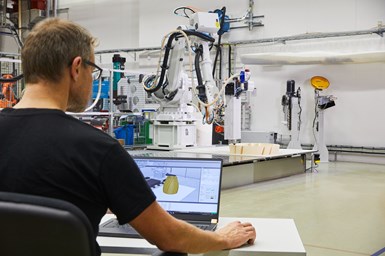
3D printing capabilities added to the robot maker’s simulation and programming system now allow for easy generation of robot paths for additive manufacturing, starting with the file output from slicer software. Photo courtesy of ABB.
The company says the new RobotStudio capabilities allow a robotic additive manufacturing program for a new part to be created in about 30 minutes. The model first is input to slicer software. (A company representative noted Simplify3D and Ultimaker’s slicer software as tools ABB team members have applied effectively.) The slicer output is then input to RobotStudio. The user needs only to choose top-level characteristics such as the robot’s target-point density (for the precision of the additive build), the speed of traverse for deposition, and the wait time between layers. Robot path programming is then written automatically.
ABB is a leading industrial robot provider; the company’s robotics division has shipped about 400,000 robot solutions, the company says, across applications including part handling and welding — and AM. Lincoln Electric Additive Solutions, a provider of additive manufacturing capability in metal, uses ABB robots in its wire-arc AM platform.
At the recent Fabtech trade show, ABB demonstrated polymer 3D printing programmed with its new software using a robot equipped with a pellet-fed extruder from Massive Dimension. Here is video filmed at that event:
Related Content
500-Pound Replacement Part 3D Printed by Robot: The Cool Parts Show #50
Our biggest metal cool part so far: Wire arc additive manufacturing delivers a replacement (and upgrade) for a critical bearing housing on a large piece of industrial machinery.
Read More3D Printing From Barstock Using Friction Stir Welding (Video)
A look at the Meld Manufacturing metal AM process. The machine tool in this video builds an additively manufactured part by rotating and compressing metal bar.
Read MoreHow Norsk Titanium Is Scaling Up AM Production — and Employment — in New York State
New opportunities for part production via the company’s forging-like additive process are coming from the aerospace industry as well as a different sector, the semiconductor industry.
Read MoreEvaluating the Printability and Mechanical Properties of LFAM Regrind
A study conducted by SABIC and Local Motors identified potential for the reuse of scrap reinforced polymer from large-format additive manufacturing. As this method increases in popularity, sustainable practices for recycling excess materials is a burgeoning concern.
Read MoreRead Next
Why Robots and Additive Manufacturing Go Together
3D printing and robots enable one another. We miss the possibilities of one if we do not consider the other. The combination includes AM for end effectors, robots for 3D printing parts, and different modes of metal and plastic production.
Read MoreFor Sustainable 3D Printed Architecture Think Renewable, Not Permanent
The design choices of today won’t be the trends of tomorrow. Aectual chooses to embrace changing tastes by making it easy to procure and recycle 3D printed architectural elements.
Read MoreThe Way Ahead for Wire Arc Additive Manufacturing
Tooling today, production tomorrow. The capability will advance as value is increasingly seen in lead time savings and design opportunities. Parts that today are cast offer a particularly promising application for a process that is “welding, except not.”
Read More