Silicon Valley-based Uniformity Labs offers an unusual proposition for powder-based metal additive manufacturing. The company, which formulates, atomizes, mixes and qualifies metal powders with its three facilities in the San Francisco Bay Area, has rejected some of the longstanding wisdom around this feedstock — namely, that the best-performing materials are batches of powders with similar particle sizes. The company has found instead that powder batches that mix particle sizes provide greater benefits for additive manufacturing.
“These are multimodal powders,” says Lalit Merani, COO at Uniformity Labs. “It’s an example of hyperuniformity, which we also see expressed in nature. Crystalline structures offer the densest packing behaviors. Our powders have randomness, increasing nodes of connection to approach crystallinity.”
“The materials are not just dense, but dense and uniform,” says Adam Hopkins, founder and CEO. “For additive manufacturers, it’s an introduction to something that might be counterintuitive to what you know.” They believe the counterintuition is worth overcoming, however, for the benefits that these multimodal powders can bring for process efficiency, material properties and more sustainable material production.
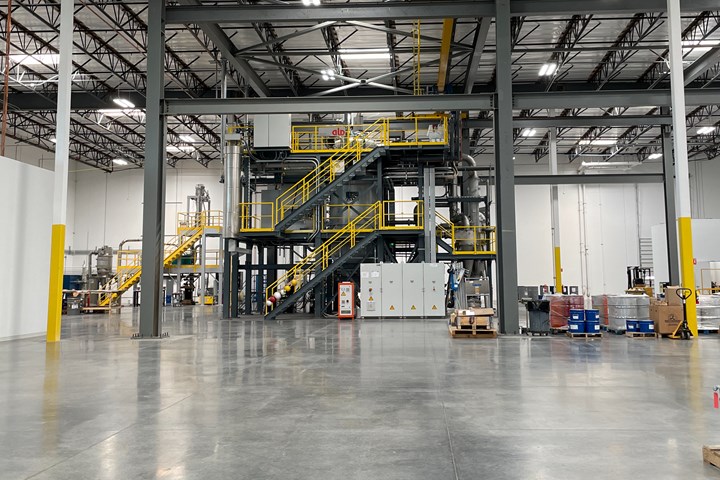
Uniformity Labs combines gas atomized powders into “multimodal” blends. The company produces about 30% of its own powders currently, using this atomizer in Fremont, California, and a second in nearby Hayward.
Uniform Density, Rather Than Size
For processes like laser powder bed fusion and binder jetting, more uniformly sized powders have been desirable for their predictable flowability and spreadability; more consistent performance within the 3D printer brings greater predictability to the final result. This perspective also influences how material is manufactured; suppliers might atomize a large amount of powder, and then select only a narrow size range or “cut” to provide to these applications, recycling or scrapping the rest.
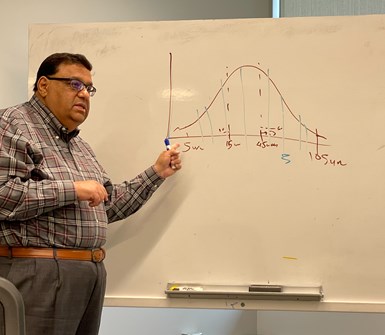
Lalit Merani, COO, describes how Uniformity Labs produces materials that combine metal powder particles of different diameters. Each product includes at least three different cuts of particle sizes.
Uniformity Labs argues instead that similar consistency in the additive manufacturing process can be achieved instead through powder density. Multimodal materials lend themselves to denser packing of the material in the powder bed, leading to workflow advantages as well as improved mechanical strength in the final parts. Plus, working with a mix or blend of particle sizes provides a use for cuts that might otherwise be scrapped.
Multimodal powders have largely not found adoption in additive manufacturing because blending powder sizes like this has implications for the flow, spreadability and recycling of the material. Powder batches that mix sizes are prone to what Merani calls the “cereal box effect”: phase separation occurs when the material is agitated, and larger particles rise to the top while smaller ones fall to the bottom. A key part of Uniformity Labs’ IP is a method for preventing this effect to ensure homogeneous, well-mixed powder throughout the entire AM workflow.
Multi-sized powders can fail to spread evenly in the print bed (left), causing inconsistency and porosity in parts. Uniformity Labs supplies multimodal powders (right) that have been designed to spread densely and uniformly, minimizing variation in 3D printing. Image Credit: Uniformity Labs
Getting the Mix Right
To create its multimodal powders, Uniformity Labs starts with materials produced through gas atomization. In this process, molten metal is dropped through a cyclone of superheated argon, which solidifies the droplets into solid spheres as they fall.
Today about 20% of this material is made in-house through the company’s gas atomizers (one located in Fremont for reactive metals, and the other, larger system in Hayward for ferrous ones). The rest of the feedstock used comes from “off-cuts” produced by other atomizers — in other words, powder made in sizes not desirable for other applications. Atomized powder is passed through a separator to capture coarse particles, then a classifier to divide out smaller ones; each desired cut of material drops into a waiting barrel.
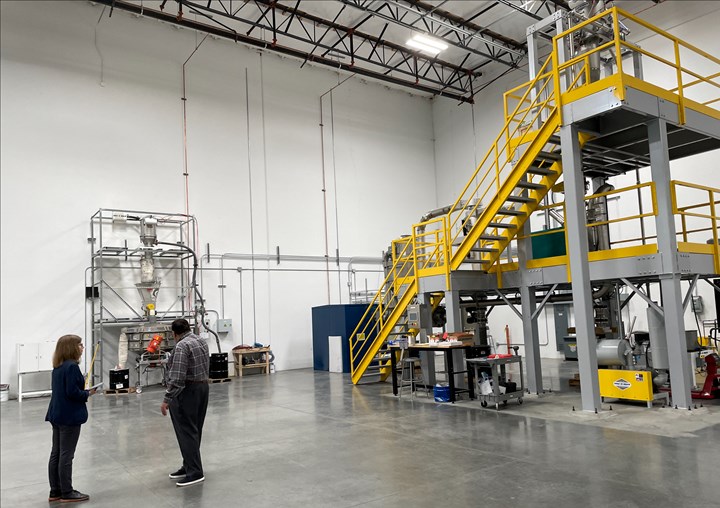
Fine powder particles are sorted with a classifier (left) and larger particles with a separator (right). All of the equipment used to atomize, sort and blend Uniformity Labs’ powders is off-the-shelf, with some custom modifications. It was important to the company to de-risk the process as much as possible, with recognizable name brand equipment and a diverse base of material sources.
Each of Uniformity Labs’ products combines three or more cuts of powder, each of which is evaluated individually in the company’s quality control lab.
To create the final mixture, cuts are combined in a dual-cone blender that uses isopropyl alcohol (IPA) solvent to heat and cool the material as it is blended. The chemical makeup of the powder doesn’t change, but through this process the particles become entropically inclined to stay mixed — behavior that holds true regardless of handling in the AM workflow.
Adam Hopkins (left), me and Lalit Merani at Uniformity Labs’ Freemont, California, facility. This blender combines the various cuts needed for each material, using heating and cooling cycles to create a multimodal powder that will stay uniformly mixed.
“The user experience is the same in terms of storage, spreadability, flowability, recycling and transportation,” Merani says.
If anything, user experience becomes slightly easier. Hopkins points out that the company’s multimodal powders tend to be less flammable and explosive than more homogenously sized batches, because of their different surface area.
“In one powder we might be using particles sizes ranging from 15 to 90 microns, where for typical laser powder bed fusion the center cut might be just 15 to 40 microns,” he says. “The oxide layer [on the outside of the powder particles] is proportional to the material’s surface area.” With a mix of powder sizes, the greater presence of large particles means the amount of surface area is less, so the overall oxide present tends to be less.
Reduced oxide also plays a role in making these powders more readily reusable and recyclable. Oxide buildup on particles of materials like titanium creates an “M&M effect” akin to the candy coating on these chocolates, increasing the material’s oxygen content as it is used — and limiting the number of times it can be reused.
“With our powders, we see less oxygen pickup over time,” Hopkins says, which translates into more possible 3D printing runs and potentially easier recycling of excess material no longer suitable for printing.
Benefits From Multimodal Powder Density
But beyond the advantages in material production and handling, Uniformity Labs and its customers have found that multimodal powders offer distinct benefits in the 3D printing process that allow for more efficient manufacturing and better results.
This automotive bracket was printed using 316L stainless steel from three manufacturers, with four different layer thicknesses all at 400-W laser power. UniFuse 316L printed at 90-micron layers provided the fastest print time, reducing total build time to nearly one-third (2.93 times) the length of time required for 40-micron layers. The UniFuse brackets also demonstrated improved yield strength, elongation and ultimate tensile strength (UTS), the company says.
In laser powder bed fusion, the more densely packed powder means that each pass of the laser melts more material in the bed without changing anything about the process parameters. But that more efficient melting behavior also makes it possible to use less energy in printing, or to speed up the laser and achieve greater productivity. The multimodal powders also lend themselves to thicker layers, providing greater speed as well as better mechanical properties, the company says.
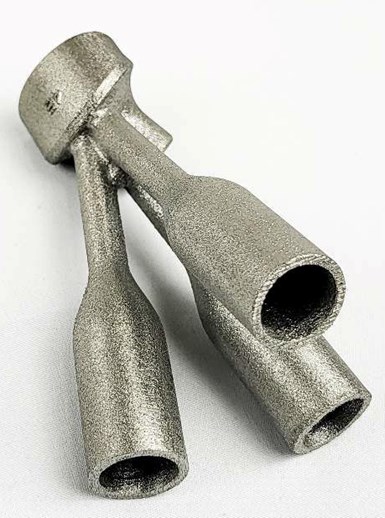
This payload bracket for a satellite assembly was 3D printed with UniFuse Ti6Al4V using SLM Solutions equipment. Using Uniformity Labs’ high-performance scanning parameters in conjunction with this material reduced the build time by 1.5 times at the same layer thickness. Read the full case study. Photo Credit: Uniformity Labs
Along with its powders, Uniformity Labs also offers recommendations for print parameters including High-Performance Scanning (HPS) guidance to take advantage of these material characteristics. UniFuse products (the company’s materials for LPBF) printed with HPS have demonstrated the capability to reduce scan time and overall build time even at thicker layers, along with advantages in mechanical performance. In many ways the benefits are limited only by the machine capabilities; as galvos get faster and printers become more efficient, Uniformity Labs’ powder advantages can “sit on top of” these improvements, Hopkins says.
While laser powder bed fusion is a significant market for Uniformity Labs today, material for metal binder jetting represents a larger share of its production and ongoing growth. For binder jetting, the more closely packed particles in the powder bed translate to smaller voids to fill; printing can therefore be tuned to use less binder for the same layer footprint, and building stronger green parts. Coupled with the flowability of the powder, users get a dual benefit in postprocessing: green parts that are easier to handle and depowder, plus unbound material that flows easily out of these parts. Binder jet parts produced with multimodal powders also shrink less in sintering, leading to less warpage and improved tolerances.
“You have to solve these problems to make binder jetting go into production,” Hopkins says.
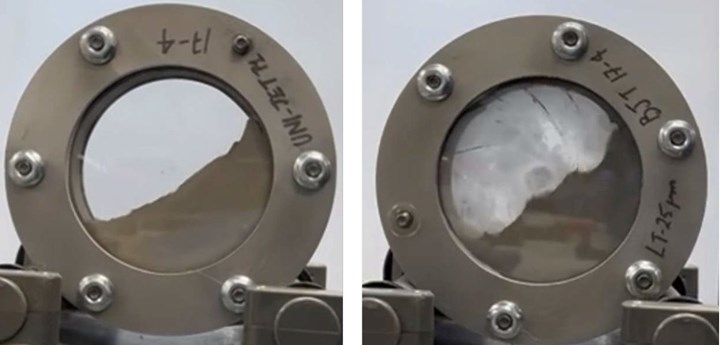
Uniformity Labs’ UniJet materials for binder jetting offer good flowability (left) compared to other options, with lower avalanche angle and ratio of avalanche to rest angle. Photo Credit: Uniformity Labs
Preparing to Accelerate With Binder Jetting
Uniformity Labs has been in operation since 2016, but did not emerge from stealth mode until 2021. That timespan is unusual for a venture capital-backed startup, especially one located in Silicon Valley. But the delay was intentional; the company did not want to launch before it was able to manufacture powders at production quantities.
“There is a trust factor that you build,” Merani says. It has been important to demonstrate to customers not only the capabilities of multimodal materials, but that Uniformity Labs can support their needs over the long term. Establishing this stability has included using proven equipment in atomization as well as sourcing off-cuts from other suppliers and partnering with machine manufacturers. The company uses feedstock from companies like Tekna in its material production, and has ongoing partnerships with equipment suppliers including Desktop Metal to develop and qualify materials for specific platforms.
Another benefit of multimodal powders in binder jetting is the ability to build fine features that can be sintered without distortion, like the honeycomb in this part featuring 0.75-mm struts. This lightweighted connecting rod concept was produced with UniJet 12-4PH stainless steel.
And production has increased dramatically over the last few years. When I visited in June of 2023, the company had already exceeded its 2022 powder output of 80 tons, and is on track to continue its growth. The greatest area of opportunity that Uniformity Labs sees now for its materials is binder jetting, especially given rising demand for electric vehicles (EVs) containing many parts suitable for production through this method.
“We’re getting to the excitement phase now,” Merani says of the 3D printing process. “Binder jetting adoption will accelerate as much or more than laser powder bed fusion.”
Related Content
Zeda AM Production Plant in Ohio Now Open — Thoughts on the New Facility
73,000-square-foot metal powder bed fusion plant includes extensive machining capability plus separate operational models for serving medical versus other businesses.
Read MoreAdditive Manufacturing Is Subtractive, Too: How CNC Machining Integrates With AM (Includes Video)
For Keselowski Advanced Manufacturing, succeeding with laser powder bed fusion as a production process means developing a machine shop that is responsive to, and moves at the pacing of, metal 3D printing.
Read MoreNew Zeda Additive Manufacturing Factory in Ohio Will Serve Medical, Military and Aerospace Production
Site providing laser powder bed fusion as well as machining and other postprocessing will open in late 2023, and will employ over 100. Chief technology officer Greg Morris sees economic and personnel advantages of serving different markets from a single AM facility.
Read MoreVariable Resistance Valve Trim Achieves Lead Time Reduction Through AM: The Cool Parts Show #69
Baker Hughes is realizing shorter lead times and simplified manufacturing through powder bed fusion to produce valve trims previously assembled from many machined metal parts.
Read MoreRead Next
Optimizing Metal Powders for Additive Manufacturing
What makes a good metal powder for additive manufacturing? Case study data highlights the value of particle size and shape, powder flowability, and bulk density.
Read MoreThe Power of the Particle: Characteristics That Affect Powder Bed Fusion AM
A recent webinar explores the influence of powder properties and the direct effect they have on AM build outcomes. Detailed are several methods for measuring characteristics of particle shape, size and surface chemistry during the feedstock life cycle.
Read MoreHybrid Additive Manufacturing Machine Tools Continue to Make Gains (Includes Video)
The hybrid machine tool is an idea that continues to advance. Two important developments of recent years expand the possibilities for this platform.
Read More