Meld Creates Spinoff Additive Printing Service Company
Meld PrintWorks Corp. will utilize Meld Manufacturing’s patented 3D printing technology to offer an additive printing service. Robb Hudson has been named CEO/president of the new company.
Meld Manufacturing Corp. has spun off a new business to create Meld PrintWorks Corp. The new company will utilize Meld’s patented 3D printing technology as an additive printing service to address the needs of multiple industries that struggle to get forgings, castings and other metal parts.
“Our customers need greater access to printed parts,” says Nanci Hardwick, Meld Manufacturing Corp. CEO. “Our Meld machine customers and prospects have universally stated a need to offer our technology as a service. We have listened and responded by providing a dedicated resource in the Meld PrintWorks Corp. Given the constraints many industries are experiencing in sourcing forgings, castings and raw materials in general, we are excited to support this transition of Meld printing technology to a production environment.”
Meld Manufacturing Corp. says it will also continue its focus on delivery of technology through machines, training and certification.
Meld PrintWorks Corp. will have a singular focus on serving customer demand for printed parts made with the Meld technology. The new company is an independent organization with separate management and operating teams. The company wasas launched in a Virginia facility separate from the current Meld Manufacturing Corp. factory.
“We spun out this company to provide a source for our many customers eager to have more access to Meld-printed parts,” Hardwick says. “We feel it important to have a hard separation between Meld Manufacturing and Meld Printworks so that the goals and focus of each company can be prioritized.”
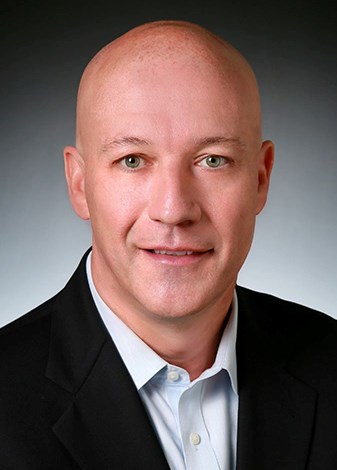
Robb Hudson has been appointed CEO and president of Meld PrintWorks. Photo Credit: Meld PrintWorks
In addition, Robb Hudson has been named CEO/president of the new company. In this position, Hudson will be responsible for ensuring PrintWorks customers receive outstanding printed parts produced with the Meld technology, on time and with a level of quality that exceeds their expectations. In this role, he will lead the PrintWorks team to meet the needs of its customers, including those who struggle to obtain forgings, castings and other metal parts due to time constraints and supply chain issues.
Most recently, Hudson served as president and CEO of Aerodyn Engineering in Indianapolis, Indiana. Previously, he also served as CEO for Mitsui Seiki USA. He has spent his career in the machine tool and manufacturing industries learning conventional and nonconventional machining processes primarily focused on the aerospace and turbine industries.
Meld Manufacturing Corp. is the inventor of the Meld process for 3D printing metal which does not melt the metal being printed. The thermo-mechanical Meld process creates enough flow in the material to combine it and create parts that otherwise appear to be forged. The process is said to versatile because it uses any metal, while it’s also simple and offers predictable results. The process is also fast, able to print large parts and has the ability to repair existing parts.
- Check out this video which looks at the Meld Manufacturing metal AM process.
- Learn how PC-based automation supports solid-state metal 3D printing using Meld Manufacturing’s 3D printing equipment.
Related Content
World’s Largest Metal 3D Printer Seen at Ingersoll Grand Opening Event
Maker of large additive and subtractive machines adds capacity in Rockford, Illinois.
Read More3D Printing Molds With Metal Paste: The Mantle Process Explained (Video)
Metal paste is the starting point for a process using 3D printing, CNC shaping and sintering to deliver precise H13 or P20 steel tooling for plastics injection molding. Peter Zelinski talks through the steps of the process in this video filmed with Mantle equipment.
Read MoreVulcanForms Is Forging a New Model for Large-Scale Production (and It's More Than 3D Printing)
The MIT spinout leverages proprietary high-power laser powder bed fusion alongside machining in the context of digitized, cost-effective and “maniacally focused” production.
Read MoreAM 101: What is Ultrasonic Additive Manufacturing?
Going from additive to subtractive can be simple with Ultrasonic Additive Manufacturing (UAM). What is it and how does it work? Learn the basics in this 101 post.
Read MoreRead Next
Video: Intelligent Layering Metal 3D Printing at 3DEO
Contract manufacturer 3DEO delivers metal parts using Intelligent Layering, a binder jetting-like 3D printing process the company developed and operates internally. Here’s how it works.
Read MoreLooking to Secure the Supply Chain for Castings? Don't Overlook 3D Printed Sand Cores and Molds
Concerns about casting lead times and costs have many OEMs looking to 3D print parts directly in metal. But don’t overlook the advantages of 3D printed sand cores and molds applied for conventional metal casting, says Humtown leader.
Read More3D Printing Brings Sustainability, Accessibility to Glass Manufacturing
Australian startup Maple Glass Printing has developed a process for extruding glass into artwork, lab implements and architectural elements. Along the way, the company has also found more efficient ways of recycling this material.
Read More