New Zeda Additive Manufacturing Factory in Ohio Will Serve Medical, Military and Aerospace Production
Site providing laser powder bed fusion as well as machining and other postprocessing will open in late 2023, and will employ over 100. Chief technology officer Greg Morris sees economic and personnel advantages of serving different markets from a single AM facility.

Zeda executives Shri Shetty (center) and Greg Morris (right) discuss the new Cincinnati-area facility with me. We are standing in front of the first-installed of what will ultimately be eight AddUp laser powder bed fusion machines in use at this site.
Contract manufacturer Zeda is outfitting a new 73,000-square-foot purpose-built facility in Springdale, Ohio, for additive manufacturing of medical implants, as well as non-medical production parts for sectors such as aircraft, defense and space.
Laser powder bed fusion (LPBF) machines from AddUp and Velo3D are being installed in the new facility, along with downstream equipment for postprocessing operations including depowdering, annealing and CNC machining. Machines from GE Additive already running in other Zeda sites will be relocated so they operate here as well.
The new facility employs 40 now, is expected to employ as many as 60 by the end of the year, and will employ over 100 at its future peak capacity, says Zeda chief technology officer Greg Morris, who oversees the new Cincinnati-area site.
Zeda is the company resulting from the merger of PrinterPrezz, a firm founded to help startup medical device manufacturers see implant products through FDA approval and into full production via AM, and the Cincinnati-area contract part producer employing AM and CNC machining, Vertex Manufacturing. The latter was co-founded by Morris.
Shri Shetty, co-founder of PrinterPrezz, is the CEO of Zeda. The merged company was formed in late 2021 and renamed in 2023. The new facility in Ohio accounts for about half of the company’s total manufacturing floorspace across three locations in the U.S. and one in Singapore, and will be the “mother ship for Zeda’s manufacturing,” he says.
Features of the plant tailored to additive manufacturing include material segregation via separate powder storage rooms for different alloys, and a quantity of electrical connections sufficient to allow postprocessing equipment to be moved freely and organized into work cells for changing production jobs. Machine layout and workflow practices proven out in this plant will provide a template for future facilities and for the globalization of Zeda’s production, Shetty says. For example, implants tailored to non-American patients (meaning both lower cost and different implant dimensions) are an important opportunity he expects AM to be able to serve.
The medical device work performed in the new facility will include implants developed in-house through PrinterPrezz’s model of working with startup inventors, as well as implants produced on a contract manufacturing basis. Combining implant production and non-implant production in the same facility is challenging, company leaders note. Work intended for implanting in the human body has to be kept segregated from work that is not, so the single plant will contain two workflow paths that will not cross. However, bringing metal part production via LPBF for such different sectors together under one roof offers advantages that easily justify the challenges of managing them, Morris says.
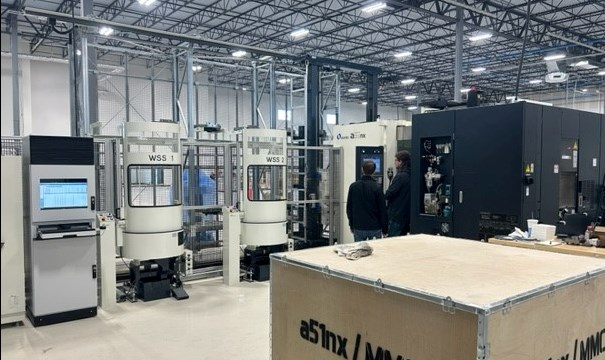
Postprocessing equipment includes CNC machine tools able to run unattended to an extent comparable to the additive machines, such as this horizontal machining center from Makino served by an automated pallet system.
Economies of scale are an obvious advantage, he notes. “Both medical and aerospace markets use titanium powder,” he says. Serving both will allow Zeda to purchase higher volumes of titanium and attain better pricing. Another potential advantage is the chance to balance capacity and income by running very different types of additive builds. “Medical implants allow us to produce a batch of parts, and we might be able to produce them in hours. A component for space might be something we produce one of, and printing it will take days,” he says. Both are potentially good business. Getting to run AM production at these two different rhythms lets them complement one another.
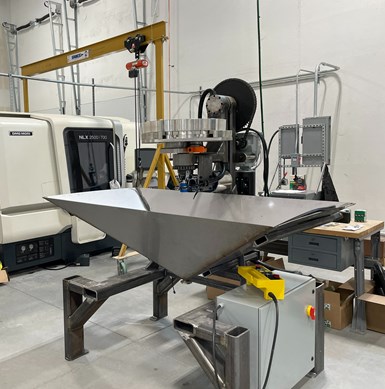
Zeda’s own team created the depowdering machine in the foreground, which will be used for large parts produced on the company’s large-capacity LPBF machines from Velo3D.
Likely the biggest advantage of developing a large additive facility serving several different markets will be the concentration of expertise the site will allow, and the cross-pollination of ideas that will result from having a team confronting and solving many different AM challenges in one place.
When the facility officially opens in the fall of 2023, says Morris, the earliest production will serve contracts for products including spinal implants and related instrumentation, as well as spacecraft parts and a component for the U.S. Department of Defense. Production on some of this work will begin ahead of the official opening while some of the facility is still being completed.
Initially, the plant’s AM resources will chiefly consist of the first five of a planned eight FormUp 350 laser powder bed fusion machines from AddUp. (AddUp’s North American headquarters is also in the Cincinnati area.) The five machines will be dedicated to Inconel 718, titanium 6-4, aluminum and 17-4 stainless steel in the case of two machines running the DoD work. In addition, the plant will have two Sapphire XC LPBF machines from Velo3D with build envelopes 600 mm in diameter by 550 mm high. Dedicated to Inconel and copper, these machines will be able to produce very large AM components for the space industry. Additional AM capacity will come when GE Additive machines including two Concept Laser M2 machines currently at the existing Vertex site and an Arcam Q10+ machine (electron beam melting) currently in California are relocated to this new facility.
Related Content
How Norsk Titanium Is Scaling Up AM Production — and Employment — in New York State
New opportunities for part production via the company’s forging-like additive process are coming from the aerospace industry as well as a different sector, the semiconductor industry.
Read MoreQualification Today, Better Aircraft Tomorrow — Eaton’s Additive Manufacturing Strategy
The case for additive has been made, Eaton says. Now, the company is taking on qualification costs so it can convert aircraft parts made through casting to AM. The investment today will speed qualification of the 3D printed parts of the future, allowing design engineers to fully explore additive’s freedoms.
Read MoreAdditive Manufacturing Is Subtractive, Too: How CNC Machining Integrates With AM (Includes Video)
For Keselowski Advanced Manufacturing, succeeding with laser powder bed fusion as a production process means developing a machine shop that is responsive to, and moves at the pacing of, metal 3D printing.
Read MoreDrones Take Flight with Metal and Polymer 3D Printed Parts: The Cool Parts Show Bonus
Drones produced by Cobra Aero now incorporate many 3D printed parts made through laser powder bed fusion and Multi Jet Fusion processes.
Read MoreRead Next
3D Printing Brings Custom, Affordable Bone Prostheses to Thai Patients
Meticuly was founded to provide custom bone implants for local patients in Thailand and regional countries who otherwise would be dependent on standard, imported devices. The concept could be a model for medical treatment in other emerging economies.
Read More4 Ways the Education and Training Challenge Is Different for Additive Manufacturing
The advance of additive manufacturing means we need more professionals educated in AM technology.
Read More3D Printing Brings Sustainability, Accessibility to Glass Manufacturing
Australian startup Maple Glass Printing has developed a process for extruding glass into artwork, lab implements and architectural elements. Along the way, the company has also found more efficient ways of recycling this material.
Read More