Improving Metal 3D Printing Processes by Reducing Support Structures
SLM Solutions’ Free Float program reduces the need for support structures, decreasing build time and powder usage, improving part quality, opening up space for more parts and giving users more design freedom.
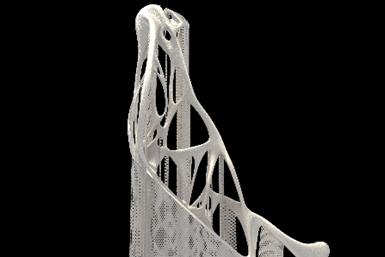
In many additive manufacturing processes, support structures are crucial for holding up features with overhangs and distributing excess heat away from parts. But support structures can also add to build times, material usage and postprocessing time, and limit design freedom. Photo Credit: SLM Solutions
Support structures play an important role in metal 3D printing — not only do they hold up overhanging features and help prevent distortion, they also absorb and distribute excess heat away from the parts during printing. However, they can also create challenges. Support structures can limit design freedom, add to build times, increase material usage, and their removal adds postprocessing time. But “Free Float,” a new software program from SLM Solutions is designed to reduce the need for support structures, providing a range of benefits.
The program started off as the by-product of a research project in 2017. It uses a vector technology that establishes thermal management by tuning laser power and other settings during the build, enabling support-free overhangs of 10 degrees on long-range geometries and 5 degrees on short-range geometries. This can decrease build time and powder usage, open up space for more parts, and give users more design freedom. It also creates a more stable melt pool in thin-walled and sharp geometries, improving part quality.
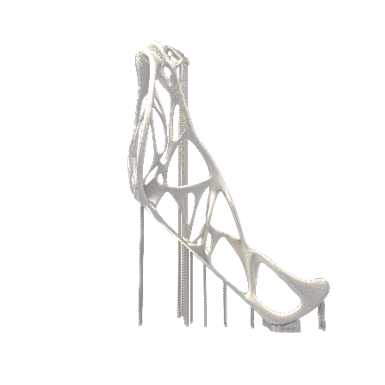
SLM Solutions’ Free Float software uses a vector technology that establishes thermal management, enabling support-free overhangs of 10 degrees on long-range geometries and 5 degrees on short-range geometries. Photo Credit: SLM Solutions
How It Works
Users upload an SLM file into the program and choose one of three profiles to apply to specific areas of the part:
- Low: Slight improvements on part quality (smoother surface, no over melting, less porosities), reduction of few necessary supports on non-critically angled sections.
- Medium: Better surface finish, increased support reduction, and medium improvements on part quality.
- High: Maximum possible reduction of supports, and improved surface finish and overall part quality.
The choice of profiles is designed to make the inerface easy to use, but there’s no “black box,” the company says; users can adjust any parameters.
Applications
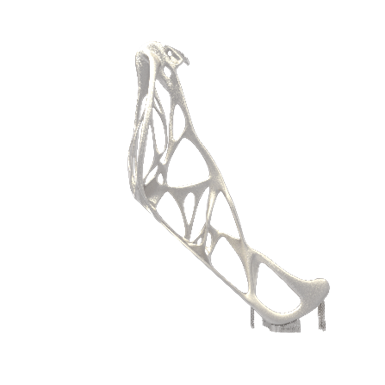
Free Float is said to decrease build time and powder usage, open up space for more parts, and give users more design freedom. It also creates a more stable melt pool in thin-walled and sharp geometries, improving part quality. Photo Credit: SLM Solutions
While the initial studies were done using steel, SLM sees the biggest potential for this technology in the aerospace and energy markers, and shifted its focus to titanium and Inconel accordingly. These are currently the only two materials available on the platform, but the company is planning on adding new materials at a rate of two per year to expand Free Float’s applications into other sectors.
Similarly, Free Float will also initially be limited to a layer thickness of 30 microns. The company says it wanted to focus first on broadening Free Float’s materials portfolio, but it plans to add more layer thickness options down the line.
The company says the basic Free Float subscription will come free of charge and is designed to be retrofittable on many of the company’s existing systems, including its 280 Production Series, 280 2.0, 500, 800 and NXG XII 600.
Related Content
Aluminum Gets Its Own Additive Manufacturing Process
Alloy Enterprises’ selective diffusion bonding process is specifically designed for high throughput production of aluminum parts, enabling additive manufacturing to compete with casting.
Read MoreAM 101: What is Ultrasonic Additive Manufacturing?
Going from additive to subtractive can be simple with Ultrasonic Additive Manufacturing (UAM). What is it and how does it work? Learn the basics in this 101 post.
Read MorePostprocessing Steps and Costs for Metal 3D Printing
When your metal part is done 3D printing, you just pull it out of the machine and start using it, right? Not exactly.
Read MoreAM 101: NanoParticle Jetting (NPJ)
The proprietary process from XJet builds ceramic and metal parts using nanoparticle suspensions. Learn how NPJ works in this introductory article, part of our AM 101 series.
Read MoreRead Next
Video: Support Structures Are Misnamed! How to Understand Anchors in Additive Manufacturing
Supports or anchors can account for a significant share of both the engineering investment and material use in metal additive manufacturing. Michael Hansen of SLM Solutions discusses the role and importance of support structures.
Read MoreCan My Machine Tool Access My Support Structures?
Analyzing the machinability of support structures opens a new way of thinking about optimal build orientation.
Read MoreRemoving Metal Supports from AM Parts
What is the best way to remove metal support structures from AM parts?
Read More