Cost per part is the major factor that will encourage adoption of additive manufacturing as a process for scale production. Improvements in machine cost, material cost and production rate will all help to bring part cost down to where it needs to be for AM to win acceptance and succeed. But at Ford Motor Company’s Advanced Manufacturing Center (AMC) in Redford, Michigan, the automaker is working on another contributor to the overall cost of production: labor. Ford AMC team members have developed and implemented an automation system now enabling round-the-clock additive production. The key was choosing the right automation — and for 3D printing, a particularly versatile and low-cost variety of automation is suitable. Today at the Redford site, an autonomous mobile collaborative robot now roams the production floor, going to the 3D printers whenever a run of parts is done.
The 3D printers that have so far been automated successfully in this way are two machines from Carbon. The autonomous collaborative robot (or cobot) is from Kuka. The two companies worked with Ford in realizing this solution, which involves communication between Kuka’s fleet management software and similar software remotely overseeing Carbon machines. Rich Moore is one of the Ford AMC team members who led the project. The number of operators involved with the 3D printers has not changed, he says — automation has not affected staffing, in part because steps such as support structure removal still need human intervention. But automation has amplified output. A mobile robot unloading parts now allows these same printers and this same team to run three to four additional builds per day on each machine.
Ford’s AMC is where future production processes are developed and proven out. The Carbon machines here run real production, just not at the volumes typical of automotive manufacturing. The machines make components for low-volume Ford vehicles (such as this Mustang Shelby GT500 parking brake bracket) as well as tooling used in mainstream production (such as a recent run of several thousand seal sizers, Moore says). Adding automation not only allows for the increase in production, it also provides a template for the production additive manufacturing system that might one day be implemented with many more 3D printers served by many more autonomous cobots.
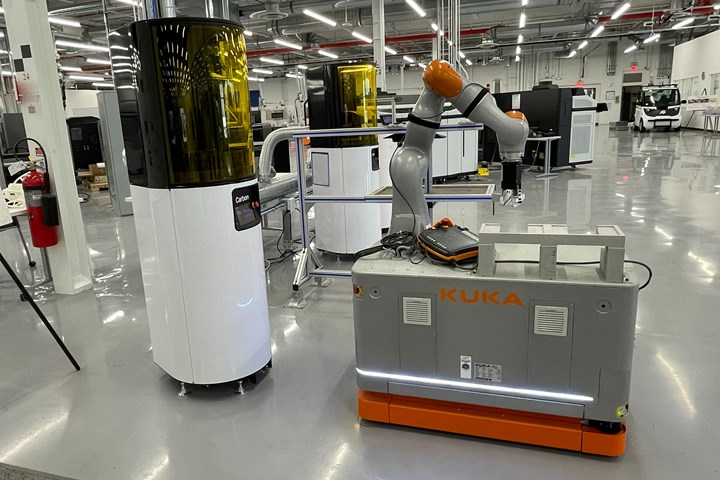
"Javier" is the mobile cobot that allows for round-the-clock 3D printing at Ford's Advanced Manufacturing Center. Ford sees this solution being scalable to a much larger number of 3D printers.
The cobot in the AMC application has been nicknamed “Javier.” It navigates the AMC facility using simultaneous localization and mapping (SLAM), a method of autonomous navigation in which the robot uses its own sensors and motion to guide its way relative to a reference zero within the facility. The collaborative robot can operate safely near people, moving with limited force and slowing or pausing motion where people are near. At the 3D printers, an additional propriety location measure Ford has patented allows the robot to precisely locate itself relative to the machine for tight repeatability in unloading build trays.
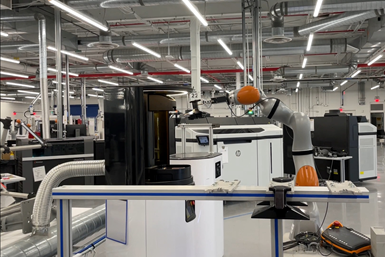
Ford worked with 3D printer maker Carbon and robot maker Kuka to develop the automated part handling. The seemingly seamless operation is the result of communication between systems from all three companies.
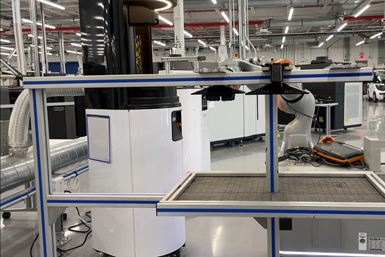
Exchanging one build tray for another is a simple step, but doing this automatically dramatically expands output. Using automation to keep on producing after people have left enables the facility to run three or four additional builds per machine per day.
Harold Sears is technical leader at the Ford AMC. He notes how the resulting model for automation is very different from what is typical of scale production. In a more typical automation approach, he says, “We might like to put a dedicated gantry or conveyor system in front of a row of 20 of these machines.” One problem with that approach is this: The dedicated automation would be — well, dedicated. Part of the reason to choose 3D printing is its redeployability as needs change, so any automation needs to be just as redeployable. But another problem Sears notes is the inefficiency of this more typical automation where AM is concerned. 3D printing cycle times are long, often hours, leaving long waits before the automation outside the cycle needs to do anything. An automation system free to roam through the plant and do other work is therefore more cost-effective. Thus, the automation system best for additive needs to be redeployable in various senses, and the Ford AMC team is looking at it this way. The next steps for the mobile cobot will include extending its role to perform other manufacturing tasks in other areas of the facility while 3D printing builds are underway.
The team in Redford is also looking toward applying the automation to other types of production 3D printing. Ford makes production parts through additive machines and processes beyond Carbon’s. Sears says the challenge to extending the automation to other AM platforms includes practical, straightforward concerns. That is, the automaker needs enough access to the machine’s control to be able to integrate it with automation, and also needs the design of the machine to facilitate robot access. For example, and this one is obvious: The machine’s build chamber should open automatically to allow for the robot. Capabilities like this are not commonplace in AM, but these changes to machine operation are coming. Just like with other manufacturing processes before it, the way ahead for additive manufacturing is automation, and that will call for machine and system considerations to accommodate this next level of productivity.
The robot makes its way safely through the facility using sensors and digital mapping. It goes to the additive machines when a build is finished and parts are ready to be removed, but during the time intervals while 3D printing is underway, it can travel to other stations in the facility to perform other handling operations.
Related Content
What Does Additive Manufacturing Readiness Look Like?
The promise of distributed manufacturing is alluring, but to get there AM first needs to master scale production. GKN Additive’s Michigan facility illustrates what the journey might look like.
Read MoreHow Large-Format 3D Printing Supports Micro-Scale Hydropower
There is potential hydroelectric power that has never been unlocked because of the difficulty in capturing it. At Cadens, additive manufacturing is the key to customizing micro-scale water turbine systems to generate electricity from smaller dams and waterways.
Read MoreDrones Take Flight with Metal and Polymer 3D Printed Parts: The Cool Parts Show Bonus
Drones produced by Cobra Aero now incorporate many 3D printed parts made through laser powder bed fusion and Multi Jet Fusion processes.
Read More3D Printing with Plastic Pellets – What You Need to Know
A few 3D printers today are capable of working directly with resin pellets for feedstock. That brings extreme flexibility in material options, but also requires greater knowledge of how to best process any given resin. Here’s how FGF machine maker JuggerBot 3D addresses both the printing technology and the process know-how.
Read MoreRead Next
3D Printing for Production at Ford: The Cool Parts Show #7
The parking brake bracket on the Mustang Shelby GT500 is now 3D printed instead of stamped. Learn how Ford is thinking about additive manufacturing in this episode of The Cool Parts Show.
Read More4 Ways Robots and 3D Printing Intersect
Four examples of how robotic automation and additive manufacturing both help and are helped by each other.
Read MoreWhy Robots and Additive Manufacturing Go Together
3D printing and robots enable one another. We miss the possibilities of one if we do not consider the other. The combination includes AM for end effectors, robots for 3D printing parts, and different modes of metal and plastic production.
Read More