What Are the Unexplored Frontiers of AM Lattice Fabrication?
A recent literature review discovered that most research into AM lattices is limited to PBF in metal and extrusion in polymer — and that experiments could be underestimating in-service lattice mechanical behavior.
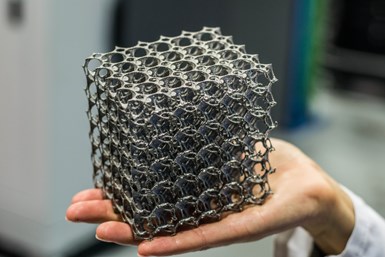
Lattices are a prime candidate for additive manufacturing due to their complex structure and intricate geometry. As a result, designers and researchers have long explored different strategies to optimize the mechanical performance of additively manufactured lattices. Solomon O. Obadimu and Kyriakos I. Kourousis’s recent literature review in Aerospace examined the state of research into additively manufactured lattices, finding several common threads and key research gaps.
The basics
Obadimu and Kourousis define lattice structures as series of repeating unit cells connected by struts and nodes in a 3D space. These structures offer lightweighting, high absorption of impact energies and a high strength-to-weight ratio. Much research surrounding AM lattices focuses on compression mechanics in an attempt to understand failure states and enhance safety.
Lattices fall into three categories, based on the degree of order of the lattice frame: periodic, pseudo-periodic and disordered. Periodic lattices have unit cells with the same shape, size and topology, arranged periodically in a 3D Euclidean space. Pseudo-periodic lattice cells share the same topology, but have different shapes and sizes. Disordered lattices, also called randomized lattices, have randomly distributed unit cells with different cell sizes and topologies. Periodic and pseudo-periodic lattice structures have customizable properties, and as such are the most common forms in engineering applications. These structures can both be further subdivided into homogenous lattices, which maintain the same strut thickness throughout, and heterogeneous lattices, where the strut thickness varies.
AM lattices appear in aerospace applications, with increasing interest from biomedical engineering, sports technology and PPE manufacturing.
Common Themes
Over the course of their literature review, Obadimu and Kourousis found that body-centered cubic (BCC) lattices are the most common type in additive manufacturing. The studies they considered featured many different methods of improving the mechanical performance of BCC lattices, and the resulting structures — with names like GBBC, ARCH and BCCZ — were all loosely based on the original BCC lattice.
As for the optimization techniques, improvements upon metal lattices largely took the form of design feature adjustments such as adding vertical members to create the BCCZ lattice model or increasing radii corners of lattice struts for the GBCC model. Non-metallic lattices often saw improvements through the adjustment of process parameters such as layer height and print angle.
The researchers included in the study tended to use triply periodic minimal surface (TPMS) and topology optimization (TOP) on metal lattices to form optimized design features. The former method is based on mathematical algorithms, while the latter is based on engineering judgement.
Lattice morphology, especially cell size and shape, has a significant effect on compressive behavior and the energy absorption capability of structures. This means that even a small shift in process parameters can create a major shift in the properties of the lattice structure. Aside from layer height and print angle, strut diameter, volume fraction and cell size also proved particularly influential toward final lattice mechanical properties.
Obadimu and Kourousis also found multiple papers suggesting the deformation process or failure mode of lattices can be improved by post-machining heat treatment, and that post-fabrication chemical treatment of lattices improve their surface roughness, energy absorption capacity and compressive strength. Other common ideas included a high correlation between relative density and lattice structures’ mechanical properties and energy absorption capability, as well as the idea that increasing the radii corners of a lattice strut will improve its energy absorption capability.
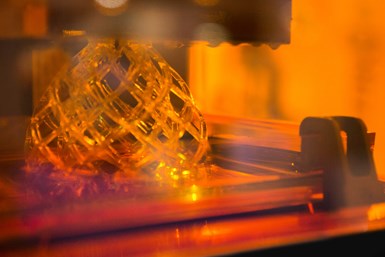
Key Insights for Future Research
Most research Obadimu and Kourousis reviewed focused on powder bed fusion (PBF) for metal lattice fabrication and material extrusion for polymer lattices. In fact, 51.92% of studies focused on PBF and 36.54% focused on extrusion, with only 5.77% for material jetting, 3.85% for binder jetting and 1.92% for vat photopolymerization. Much space remains for future researchers to explore alternative methods for additively manufacturing lattice structures.
Even extrusion offers fertile ground for further research, with few studies examining metal AM via extrusion. Obadimu and Kourousis suggest the lack of exploration in this particular territory is a result of ongoing concerns about challenges such as first-layer adhesion, warping, shrinkage and support structure removal. The two see potential progress in several studies from Kumar et al. focusing on the use of a supportless “sea urchin” lattice structure — but while Obadimu and Kourousis believe this lattice shows promise, they also underscore the need for further research into its mechanical properties.
The research also suggested that AM repeatability and fabrication-induced divergences from CAD models are a continuing concern for AM lattice fabrication. While process parameter adjustment and post-processing machining can address some of these concerns, Obadimu and Kourousis call for additional research into the improvement of AM repeatability.
One last, crucial observation regarded the accuracy of experimental results. While experimental results and finite element simulations largely showed good agreement across the studies, both methods of verification could underestimate in-service mechanical behavior. Obadimu and Kourousis cited one study from Shen et al., which found that lubricating plates prior to conducting compression tests reduced the effect of friction on mechanical compression testing results. Obadimu and Kourousis join Leary et al. in calling for AM researchers and designers to stay cognizant of these sorts of process variables during experimental analysis.
Related Content
3D Printed Ceramic Mug: The Cool Parts Show #48
MadeXBinary applies additive manufacturing to clay. The company achieves automated production of aesthetically pleasing kitchenware through digital pottery.
Read More3D Printed "Evolved Structures" for NASA Exoplanet Balloon Mission: The Cool Parts Show #61
Generative design creates stiff, lightweight brackets for EXCITE mission monitoring planets orbiting other stars. The Cool Parts Show visits Goddard Space Flight Center.
Read MoreImplicit Modeling for Additive Manufacturing
Some software tools now use this modeling strategy as opposed to explicit methods of representing geometry. Here’s how it works, and why it matters for additive manufacturing.
Read MoreSeurat: Speed Is How AM Competes Against Machining, Casting, Forging
“We don’t ask for DFAM first,” says CEO. A new Boston-area additive manufacturing factory will deliver high-volume metal part production at unit costs beating conventional processes.
Read MoreRead Next
3D Printing Brings Sustainability, Accessibility to Glass Manufacturing
Australian startup Maple Glass Printing has developed a process for extruding glass into artwork, lab implements and architectural elements. Along the way, the company has also found more efficient ways of recycling this material.
Read MoreVideo: Intelligent Layering Metal 3D Printing at 3DEO
Contract manufacturer 3DEO delivers metal parts using Intelligent Layering, a binder jetting-like 3D printing process the company developed and operates internally. Here’s how it works.
Read MoreLooking to Secure the Supply Chain for Castings? Don't Overlook 3D Printed Sand Cores and Molds
Concerns about casting lead times and costs have many OEMs looking to 3D print parts directly in metal. But don’t overlook the advantages of 3D printed sand cores and molds applied for conventional metal casting, says Humtown leader.
Read More