Another Giant Leap for AM — New Standards
Did anyone notice how many AM standards got approved during the pandemic?
With everything going on these past 18 or so months, many manufacturers probably missed all the new standards that emerged — but then again, who waits with bated breath for new standards to be released? Certainly not most engineers or designers, but in additive manufacturing (AM), new standards help bring semblance of order and clarity to a burgeoning and chaotic field.
Why the flurry of AM standards? With everyone in lockdown and unable to travel, maybe the pandemic actually helped accelerate standards development. I mean, why wait for a face-to-face meeting when its possible to simply hop on Zoom anytime from anywhere and debate the wording on the latest standard in development? Or maybe all of the committee members were able to be present, discuss, revise and approve new standards much more rapidly with fewer distractions? Who knows exactly what happened and why, but the output has been a boon for AM. Now the challenge is keeping up with them all.
While ASTM/ISO have published the most AM standards, SAE International wins the prize for most active Standards Development Organization (SDO) the past 18 months in my opinion. Specifically, its Aerospace Materials Specification (AMS) AM Additive Manufacturing Metals Committee has issued 11 new standards since January 2020. While many of these are for powder feedstocks used in aerospace AM applications, the committee has also released standards for wire-fed directed energy deposition (DED) for both laser (AMS 7010), electron beam (AMS 7027) and electron beam powder bed fusion (AMS 7007), as well as binder jetting (AMS 7022). Meanwhile, 19 additional standards are listed as works in progress, including a standard practice for designing AM components in an aircraft system (AMS 7042) — one that I am anxiously awaiting, given my design for AM (DfAM) interests. Wait, did I just write that I was anxiously awaiting a standard? I am such a geek.
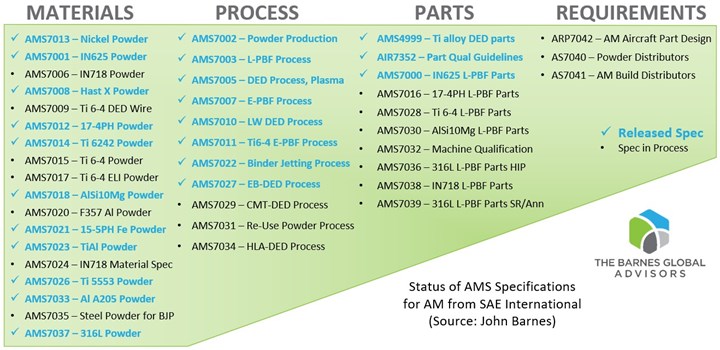
Summary of Aerospace Materials Specification (AMS) Standards for AM approved and in development by SAE International. Photo Credit: John Barnes, The Barnes Global Advisors
NASA
In addition to these 30 – yes, 30! – issued and forthcoming standards for AM aerospace applications, NASA released its Additive Manufacturing Requirements for Spaceflight Systems (NASA-STD-6030) in April 2021. This new standard creates NASA-wide requirements for AM and is accompanied by NASA-STD-6033, which specifies requirements for equipment and facility control for additive manufacturing. As such, it provides a clear pathway for qualifying and certifying AM parts for spaceflight. Right before the pandemic, I was lucky enough to see Mars 2020 Perseverance, which carries 11 metal AM parts, undergoing testing shortly before it was launched, and I still remember flying back home from that trip wondering why so many people were wearing face masks in LAX.
Aerospace Industries Association
Another document for AM qualification and certification is the Recommended Guidance for Certification of AM Components, which was issued by the Aerospace Industries Association (AIA) Additive Manufacturing Working Group in February 2020. It is freely available online and provides useful guidance on process control documentation, operator training and software configuration control, as well as supply chain qualification for AM. Its guidance on material property development for AM was particularly easy to digest, as was the corresponding discussion on part design and qualification.
European Federation of Welding, Joining, and Cutting
Speaking of AM operator training, I recently learned that the European Federation for Welding, Joining, and Cutting (EWF) leveraged its training, qualification and certification system for welding personnel to create three levels of certification for AM operators and four levels of certification for AM engineers. The graphics on EWF’s AM website are easy to navigate, and the accompanying information provides a good reference or starting point for any company new to AM.
ASTM
ASTM remains very active as well, with AM standards efforts coordinated and supported by its Additive Manufacturing Center of Excellence. ASTM’s E07 Nondestructive Testing Committee released the Standard Guide for Nondestructive Examination of Metal Additively Manufactured Aerospace Parts After Build (ASTM E3166) in August 2020. This standard provides a wealth of information on a variety of nondestructive evaluation technologies, including radiographic and x-ray computed tomography, eddy current evaluation, penetrant testing, thermographic testing, process compensated resonance testing, ultrasonic testing and optical metrology.
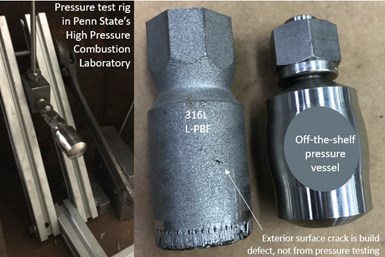
Pressure test rig (left) along with AM (middle) and off-the-shelf (right) pressure vessels in 316L stainless steel after testing; the AM pressure vessel did not deform (like the conventional one) nor burst under 2.5 times the rated load. Photo Credit: David Drewniak and Nick Nace, Penn State
Finally, the reason why I had pressure vessels on my mind last month: ASME issued its new standard, Criteria for Pressure Retaining Metallic Components Using Additive Manufacturing (PTB-13-2021) in May 2021. The standard outlines procedures for specifying and qualifying AM pressure vessels and includes details on testing procedures and witness sampling as well as chemical composition analysis, mechanical property testing and metallographic evaluation. Personally, I would rather just print some and pressurize them until they blew up, but my graduate student and I tried that and maxed out the pressure in the test rig in Penn State’s High Pressure Combustion Lab (thanks David Drewniak for your help testing and SLM Solutions for printing test samples for us). We saw no sign of deformation even at 2.5 times the rated load; so, I guess we accidently overdesigned the AM pressure vessel when we modified the shell’s interior to eliminate support structures. I wish we had had ASME’s standard earlier — or the support-free AM capability I discussed last month!
Related Content
Velo3D Founder on the 3 Biggest Challenges of 3D Printing Metal Parts
Velo3D CEO and founder Benny Buller offers this perspective on cost, qualification and ease of development as they apply to the progress of AM adoption in the future.
Read MoreDrones Take Flight with Metal and Polymer 3D Printed Parts: The Cool Parts Show Bonus
Drones produced by Cobra Aero now incorporate many 3D printed parts made through laser powder bed fusion and Multi Jet Fusion processes.
Read MoreImplicit Modeling for Additive Manufacturing
Some software tools now use this modeling strategy as opposed to explicit methods of representing geometry. Here’s how it works, and why it matters for additive manufacturing.
Read More3D Printed Ceramic Mug: The Cool Parts Show #48
MadeXBinary applies additive manufacturing to clay. The company achieves automated production of aesthetically pleasing kitchenware through digital pottery.
Read MoreRead Next
At General Atomics, Do Unmanned Aerial Systems Reveal the Future of Aircraft Manufacturing?
The maker of the Predator and SkyGuardian remote aircraft can implement additive manufacturing more rapidly and widely than the makers of other types of planes. The role of 3D printing in current and future UAS components hints at how far AM can go to save cost and time in aircraft production and design.
Read MoreHybrid Additive Manufacturing Machine Tools Continue to Make Gains (Includes Video)
The hybrid machine tool is an idea that continues to advance. Two important developments of recent years expand the possibilities for this platform.
Read More3D Printing Brings Sustainability, Accessibility to Glass Manufacturing
Australian startup Maple Glass Printing has developed a process for extruding glass into artwork, lab implements and architectural elements. Along the way, the company has also found more efficient ways of recycling this material.
Read More