Micro 3D Printing Slashes Costs, Lead Time for Medical Part
Micro 3D printing enabled AntiShock to produce a small-dimension, high-detail part with greater accuracy than SLA and at 20% of the cost of CNC production.
Share
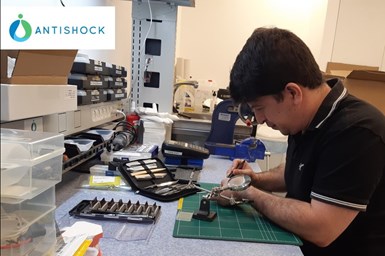
Dmitri Khalilov, cofounder and CTO at AntiShock Labs.
Photo Credit: 3D Evaluate
AntiShock is a medical device start-up company whose headlining product is a disposable, non-invasive, continuous monitoring system that measures patients’ systemic fluid responsiveness to prevent intravenous fluid (IV) overload. Fluid overload is a common condition among intensive care unit (ICU) patients that can cause organ failure and, in severe cases, death.
To further improve its solutions to this problem, AntiShock is developing an electro-optical sensing medical device based on a tiny electro-optical sensor. This sensing device is built out of several small mechanical moving components with high strength and accuracy requirements. Therefore, to validate its product and produce a working prototype device, AntiShock turned to advanced manufacturing technologies.
AntiShock initially considered CNC machining and the stereolithography (SLA) 3D printing process that created the first product mock-up. However, when confronted with the need to produce a small-dimension, high-detail component about 1 mm in diameter, available SLA technology could not provide the required levels of details and accuracy. CNC machining could produce these parts, but the resulting per-part cost was expensive.
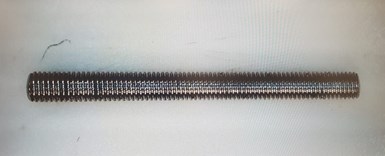
The threaded screw inside AntiShock’s medical device. Photo Credit: AntiShock
Micro 3D Printing
While searching for a solution to this problem, Dmitri Khalilov, co-founder and CTO of AntiShock, came across Nanofabrica’s micro 3D printing system. Curious and intrigued, Khalilov made contact with Avi Cohen, Nanofabrica’s executive vice president of sales, presenting the challenge of producing AntiShock’s small-dimension, high-detail component.
The challenge went beyond printing the component: the part needed a non-standard-pitch thread that could fit a small screw on top of it, the components had to fit each other perfectly, and the final component had to be strong enough to sustain mechanical loads.
After reviewing the part’s size, geometry and thickness, and estimating the mechanical loads the part needed to withstand, Nanofabrica accepted the challenge. Only a few days after delivering a CAD file, the AntiShock R&D received a complete, 3D printed prototype. The team swiftly moved to evaluate the part’s accuracy and verify the production of the required details. The part passed with flying colors — and fit the small metal screw.
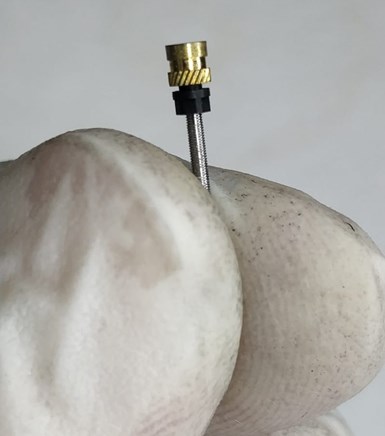
The micro 3D printed part for AntiShock’s medical device fit perfectly onto the small metal screw. Photo Credit: AntiShock
The Benefits of Micro 3D Printing
After reviewing the data, AntiShock concluded micro 3D printing offered distinct advantages in various areas.
First, micro 3D printing had the ability to provide the challenging levels of detail and accuracy required, even at resolutions too small for traditional 3D printing. Micro 3D printing also promotes design freedom, and so facilitated the production of AntiShock’s part without many of the design limitations baked-in with conventional production processes. The delivery time for five 3D printed parts was one day, whereas delivery times with CNC would have been between three to four days. Micro 3D printing also saved 80% on costs compared to CNC’s several hundreds of dollars.
Final Conclusions
Less than a week after beginning work with Nanofabrica’s micro 3D technology, AntiShock’s team solved their problem. The possibility of micro 3D printing opened up a wide range of R&D possibilities for AntiShock regarding its existing and future devices. Micro 3D printing also integrated well with AntiShock’s existing to CNC and SLA 3D printing workflow, as these other production methods produced device’s larger parts.
Related Content
3D Printing with Plastic Pellets – What You Need to Know
A few 3D printers today are capable of working directly with resin pellets for feedstock. That brings extreme flexibility in material options, but also requires greater knowledge of how to best process any given resin. Here’s how FGF machine maker JuggerBot 3D addresses both the printing technology and the process know-how.
Read MoreDMG MORI: Build Plate “Pucks” Cut Postprocessing Time by 80%
For spinal implants and other small 3D printed parts made through laser powder bed fusion, separate clampable units resting within the build plate provide for easy transfer to a CNC lathe.
Read MoreNew Electric Dirt Bike Is Designed for Molding, but Produced Through 3D Printing (Includes Video)
Cobra Moto’s new all-electric youth motocross bike could not wait for mold tooling. Parts have been designed so they can be molded eventually, but to get the bike to market, the production method now is additive manufacturing.
Read MoreHow Siemens Energy Applies Additive Manufacturing for Power Generation and More
At an applications center in Orlando, Florida, a small team of AM specialists is spanning industries by 3D printing parts to support both Siemens Energy power generation systems and external customers.
Read MoreRead Next
3D Printing Brings Sustainability, Accessibility to Glass Manufacturing
Australian startup Maple Glass Printing has developed a process for extruding glass into artwork, lab implements and architectural elements. Along the way, the company has also found more efficient ways of recycling this material.
Read More4 Ways the Education and Training Challenge Is Different for Additive Manufacturing
The advance of additive manufacturing means we need more professionals educated in AM technology.
Read MoreHybrid Additive Manufacturing Machine Tools Continue to Make Gains (Includes Video)
The hybrid machine tool is an idea that continues to advance. Two important developments of recent years expand the possibilities for this platform.
Read More