Share
Read Next
Additive manufacturing (AM) in metals looks fundamentally different from machining, even down to the raw material. Where AM transforms wires and powders into geometries that bear little resemblance to their original forms, the machining world deals in castings, forgings, billets and barstock, and works to reveal the part inside the material within the constraints of its original shape and size.
But those solid pieces of material have distinct advantages over the powdered metals used in many additive processes. They do not require specialized storage vessels or safety measures the way that reactive metal powders do. They are less susceptible to the effects of temperature fluctuations or humidity. They are readily available. And perhaps most strikingly, they are far less expensive than powders intended for additive manufacturing.
It’s this last point — the economics of powdered metals — that first prompted John Barnes and Chris Aldridge to begin exploring how these materials might be made differently. With industry experience at places such as Lockheed Martin, Honeywell and Arconic, the two were well positioned to develop the process that would become the crux of a new business, Metal Powder Works. The company’s DirectPowder proprietary process transforms metal barstock or other solid material into powders suitable for additive manufacturing. The process is flexible, controllable and offers valuable material property characteristics — in addition to being more affordable than other methods for producing these materials.
Metal Powders from Barstock
Most metal powders available for 3D printing methods such as powder bed fusion and binder jetting are today made with gas atomization. Large amounts of metal are melted and passed through a controlled gas flow to create small particles that are then sieved into various sizes for different processes. Gas atomization was built for scale production, Barnes says, which means expensive startup costs and limited control over particle size distribution and morphology. The process also produces waste — inevitably when sieving is complete, there will be powder leftover that may not be sellable.
“In many cases atomizing is the right answer. There are markets for all different size distributions of a material like Inconel 718,” Barnes explains. “It’s not such a great process for newer materials, or where you don’t have a market for all the different sizes. Titanium is a perfect example — there really isn’t much of a market for the oversized powder.”
Rather than try to optimize or change the gas atomization process, Metal Powder Works has developed a different way of producing metal powders that does not rely on gas or gravity. Its DirectPowder process is entirely mechanical and requires no melting. Instead, a piece of feedstock material is rotated against proprietary tooling that removes millions of metal particles per second, something like a lathe that has been optimized not for efficient material removal but for precise chip control. Computer algorithms drive the process, controlling the particle size and morphology of the resulting powder particles. The method can use affordable barstock and billet, and is cheaper than atomization for smaller batches of material.
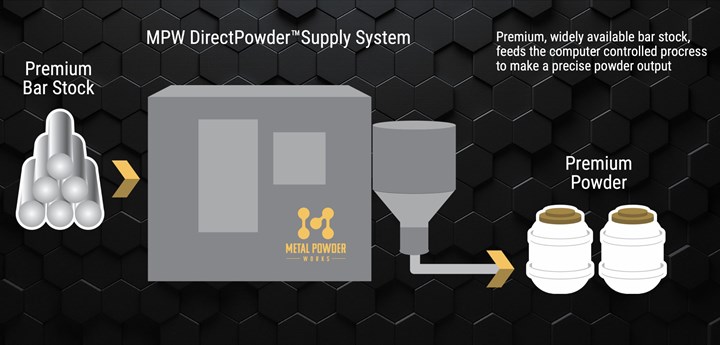
Metal Powder Works’ DirectPowder supply system transforms barstock into powders suitable for metal 3D printing. Images: Metal Powder Works
“If you’re looking at a 7075 product today, let’s say it sells for $75 a pound,” Barnes says by way of illustration. “Barstock sells for about $6 a pound. And by the way, barstock is not pyrophoric. It doesn’t pick up humidity, it’s safe, it’s easy to ship around, and you can pretty much buy it anywhere with certifications. People could be buying barstock, and they’ll never buy powder again.”
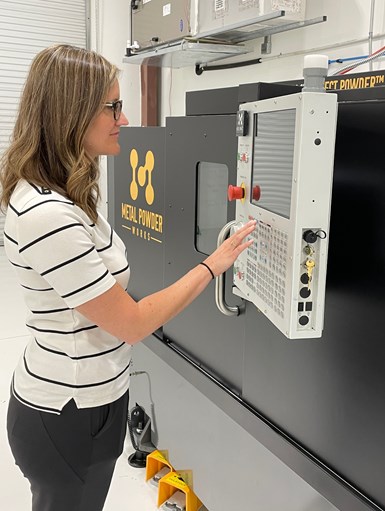
The DirectPowder process takes place at room temperature, with no need for inert gas or other safety measures common to atomization.
But the DirectPowder technique offers other significant advantages beyond cost reduction. Using off-the-shelf feedstock means that more manufacturers will be able to make the leap to additive using exactly the same materials they are already used to, just applied in a different process. The method is highly efficient and creates very little waste; the particle size and morphology can be more precisely controlled to produce just the grade of powder needed, no sieving required. The solid-state process takes place at room temperature with no melting of the material, and requires no inert gas. DirectPowder is safer overall than atomization, and also provides material property benefits by maintaining certain characteristics of the feedstock.
“We generally preserve the temper of the bar we start with,” Barnes says. “For a fusion-based process this may not matter, but for processes like cold spray which are solid state, different tempers give you different deposition efficiencies.”
On-Demand Powder for Expeditionary Manufacturing
This last point is especially relevant to Metal Powder Works’ recently announced collaboration with Spee3D, the Australian provider of supersonic 3D deposition (SP3D) equipment. Spee3D’s printers use compressed air to spray powdered metal onto a build platform manipulated by a robot arm, allowing for the creation of complex geometries without support structures. The process is fast, material efficient, and a viable alternative to forgings and castings.
Like DirectPowder, SP3D occurs at room temperature and does not require inert gas, both factors that have led the Australian army to experiment with expeditionary manufacturing using this platform. Royal Australian Electrical and Mechanical Engineers (RAEME) craftsmen from the Australian Army have successfully designed and manufactured more than 50 parts using the WarpSpee3D printer during field trials of this technology. But deploying a mobile 3D printer means keeping it stocked with material, and for reactive metal powders, keeping that material dry, safe and properly packaged to ensure it is usable when needed.
DirectPowder represents a way around the storage and handling challenges. Metal Powder Works has partnered with Spee3D to develop Project Sidecar, an initiative that pairs a SP3D printer with a mobile DirectPowder unit that can feed newly created powders directly into the cold spray process. As an additional benefit, the output of the DirectPowder Sidecar unit nearly matches the consumption of the Spee3D printer, meaning there is little or no excess powder created. Rather than carry canisters of powdered metals, military units and other users could simply transport or procure solid blocks of material on location, enabling easier and safer in situ, expeditionary manufacturing.
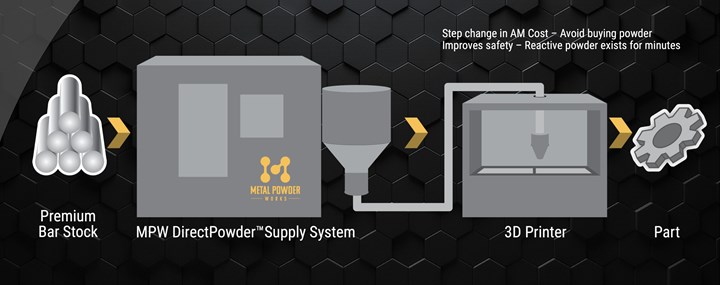
The DirectPowder system can be connected directly to a 3D printer, such as Spee3D’s cold spray platform, to minimize the risks associated with metal powder creation and handling.
Technology and Accounting
For its metal powder production and process development activities, Metal Powder Works currently operates two DirectPowder systems at a facility in Austin, Texas. So far the technique has been proven for aluminum and copper, but the company is experimenting with other materials including (despite its metal origins) high-temperature polymers such as PEEK.
“There are many levers we can play with to achieve different things,” Barnes says. “Because we’re doing this with numerical control instead of gravity, we have an inordinate amount of control over the process.” Manipulating the speed of the rotating material and other variables can adjust the powder size and morphology, as well as tune DirectPowder to new materials and the needs of other AM processes. The company is also working to develop a more robust system that will be capable of processing harder metals. Not every material will be compatible with the method or with additive manufacturing, but that’s part of the advantage of no-melt powder production: Small batches are more affordable, and it costs less to find out.
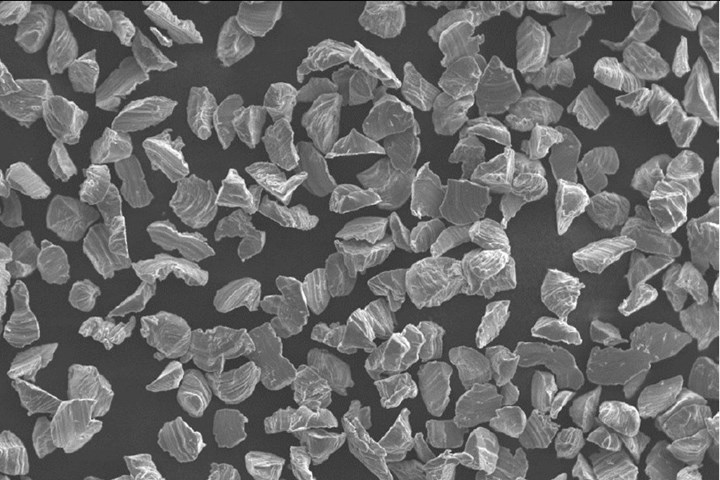
“There are many levers we can pull” to acheive the desired size and morphology of the resulting metal powder, John Barnes says. DirectPowder materials do not require sieving, as they are produced just in the size range needed.
Longer term, Metal Powder Works plans to distribute its powder production technology closer to the places where that powder will be used through efforts like Project Sidecar and a forthcoming offering called Powder by the Hour, a leasing program to place DirectPowder systems at additive manufacturing locations. Service bureaus and other users will be able to pay by the hour to transform barstock and other materials into powders for 3D printing. Affordable, on-demand powders produced onsite could help make additive manufacturing overall more accessible by reducing both the cost and complexity of using this material.
“When you keep these buckets of powder laying around, it’s very expensive inventory,” Barnes says. “When you keep bars of material around, it’s still inventory — but it’s less expensive inventory that doesn’t care so much about the temperature and the humidity.”
Related Content
Multimaterial 3D Printing Enables Solid State Batteries
By combining different 3D printing processes and materials in a single layer, Sakuu’s Kavian platform can produce batteries for electric vehicles and other applications with twice the energy density and greater safety than traditional lithium-ion solutions.
Read MoreWhat Does Additive Manufacturing Readiness Look Like?
The promise of distributed manufacturing is alluring, but to get there AM first needs to master scale production. GKN Additive’s Michigan facility illustrates what the journey might look like.
Read MoreAt General Atomics, Do Unmanned Aerial Systems Reveal the Future of Aircraft Manufacturing?
The maker of the Predator and SkyGuardian remote aircraft can implement additive manufacturing more rapidly and widely than the makers of other types of planes. The role of 3D printing in current and future UAS components hints at how far AM can go to save cost and time in aircraft production and design.
Read MoreAluminum Gets Its Own Additive Manufacturing Process
Alloy Enterprises’ selective diffusion bonding process is specifically designed for high throughput production of aluminum parts, enabling additive manufacturing to compete with casting.
Read MoreRead Next
Printing Solid, Simple Metal Parts in Minutes, Spee3D Process Is Competition for Casting
Kinetic energy additive process bonds metal not through melting, but with the use of compressed shop air.
Read MoreMaking a Slow Decision on a Fast Technology: Evaluating the Business Case for Multi-Laser Powder Bed Fusion
A data-driven approach to laser powder bed fusion reveals how companies can get cost out of parts and match productivity to customer requirements. Part Three of a three-part series.
Read MoreDistribution Network Aims to Be the "Inventory Bridge" for Metal Powders
Recently launched KBM Advanced Materials connects metal powder suppliers to customers in additive manufacturing, metal injection molding and more.
Read More