GE Earns Air Force Airworthiness Qualification for Critical Jet Engine Part
Pathfinder with the USAF’s Propulsion Directorate and Rapid Sustainment Office (RSO) gathers momentum as it establishes its own qualification path for additively manufactured metal parts.
Share
Read Next
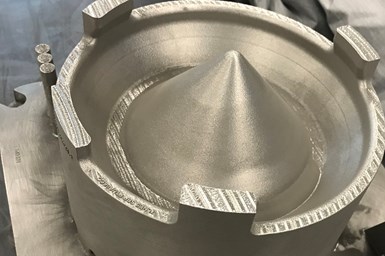
The cobalt-chrome sump cover for F110 engine was additively manufactured on a GE Additive Concept Laser M2 machine at the GE Additive Technology Center in Cincinnati, as part of collaboration with the U.S. Air Force’s Rapid Sustainment Office.
GE Aviation has received Engineering Change Proposal (ECP) approval from the U.S. Air Force (USAF) for an F110 additively manufactured sump cover. The F110 component is the latest milestone in the USAF and GE’s pathfinder Pacer Edge program and is the first engine component designed for and produced by metal additive manufacturing (AM) to be qualified by any U.S. Department of Defense entity.
“Much like the GE90 T25 sensor that was an FAA certification pathfinder for metal additive manufacturing for GE Aviation in commercial aerospace, the F110 sump cover sets a solid foundation for many more additively manufactured component qualifications with GE’s military customers,” says Matt Szolwinski, chief engineer and leader of GE’s Large Military Engineering team.
The company says that the Pacer Edge program is an important initiative for reducing risk and showcasing the application of AM in aerospace. “The ability to additively manufacture an aircraft engine part and gain military airworthiness is a significant step forward in growing the adoption of additive manufacturing in the Air Force,” says Nathan Parker, deputy program executive officer for the USAF RSO.
The Chief of Staff of the Air Force has challenged the group to ‘accelerate change or lose.’ “The entire Pacer Edge process is built around the ‘accelerate change’ philosophy, and the speed of the F110 sump cover development and airworthiness approval is evidence of that,” says John Sneden, director of the USAF’s Directorate of Propulsion. “The capability that Pacer Edge is demonstrating and proving will be a game changer to engine production and sustainment and will resolve many future Air Force readiness challenges.”
The company says that part of the key to the accelerated qualification — in under a year — was GE’s decade of metal additive engineering and manufacturing expertise. The team’s in-depth knowledge of commercial aerospace engine airworthiness for flightworthy 3D printed metal parts is proving instrumental in helping the USAF establish its own robust process validation and certification processes for military airworthiness.
Related Content
-
Inspection Method to Increase Confidence in Laser Powder Bed Fusion
Researchers developed a machine learning framework for identifying flaws in 3D printed products using sensor data gathered simultaneously with production, saving time and money while maintaining comparable accuracy to traditional post-inspection. The approach, developed in partnership with aerospace and defense company RTX, utilizes a machine learning algorithm trained on CT scans to identify flaws in printed products.
-
Making Sense of Qualification, Certification and Standards in Additive Manufacturing: AM Radio #48
AM needs standards and processes for qualification and certification just like any other process. In this conversation with Dr. Tim Simpson, AM editors dive into the distinctions between these terms, and explore how they are influencing additive adoption and advancement.
-
Additive Manufacturing in Space: Failing Upward
Not all 3D printed parts destined for space need to adhere to the standards of human space flight. Yet all parts made for space programs require some type of qualification and certification. NASA and The Barnes Global Advisors explore Q&C for these parts.